I am trying to assess the capacity of a steel I girder (on a bridge) that has been struck by an over-height vehicle, causing the bottom flange to be quite deformed locally with a sharp indentation in its edge - see photo below.
If it were the case of a bolt hole in the bottom flange, there would be no issue here. As the beam approaches its plastic section capacity, there would be localised yielding and strain hardening around the hole with associated load redistribution, the end effect being that the full plastic section capacity of the beam could be realised. The Australian codes allow this, provided that the combined area of the holes does not exceed a certain fraction of the flange area, this fraction depending on the yield and tensile strength of the material.
However, where there is a sharp notch in the side of a ductile element (sharp being the important word here), my understanding is that there can be a significant reduction in ductility.
Could this be enough to cause the beam not to reach its plastic section capacity (i.e. fail in some other way, perhaps more along the lines of a tearing type failure?)
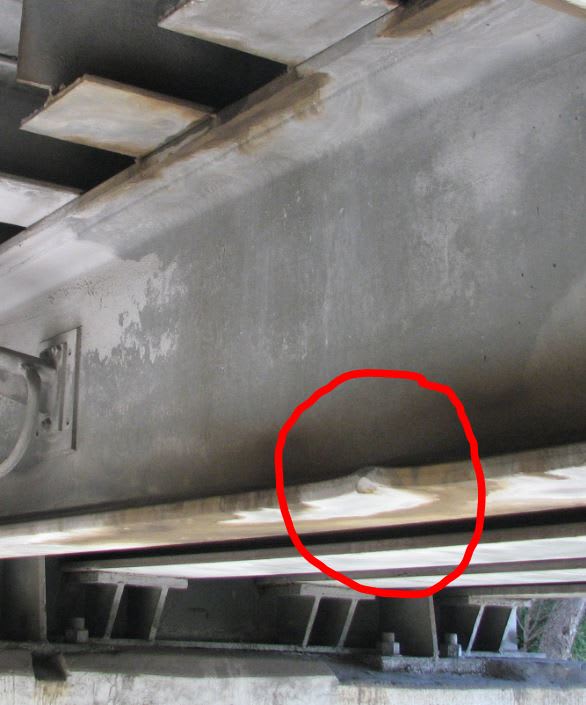
If it were the case of a bolt hole in the bottom flange, there would be no issue here. As the beam approaches its plastic section capacity, there would be localised yielding and strain hardening around the hole with associated load redistribution, the end effect being that the full plastic section capacity of the beam could be realised. The Australian codes allow this, provided that the combined area of the holes does not exceed a certain fraction of the flange area, this fraction depending on the yield and tensile strength of the material.
However, where there is a sharp notch in the side of a ductile element (sharp being the important word here), my understanding is that there can be a significant reduction in ductility.
Could this be enough to cause the beam not to reach its plastic section capacity (i.e. fail in some other way, perhaps more along the lines of a tearing type failure?)