What is the interpretation of net section area for shear lag when there is an HSS (cut in half) or a channel section welded as per below?
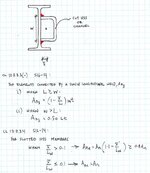
- CL 12.3.3.3(b) is for "elements connected by longitudinal welds along two parallel edges". But, are the toes of the channel or top/bot of a cut HSS considered two parallel edges?
- CL 12.3.3.3(c) is for "elements connected by a single longitudinal weld". In this case the efficiency factor is dependent on w (depth of HSS or depth of the channel).
- CL 12.3.3.4 is for "...rectangular HSS members [slotted] and welded to a plate". In this case the efficiency factor is dependent on x_bar only.
- Total weld length (e.g. # of stitchs x stitch length) or the required length for an equivalent stitch weld?
- Total connection length (e.g. total length from first stitch to last stitch)?
- Length of 1 stitch? If so, I would imagine the net section would need to be multiplied by the number of stitches...so possibly getting a big reduction factor that comes out in the wash once you consider the total stitches
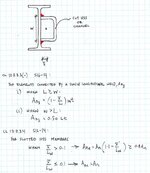