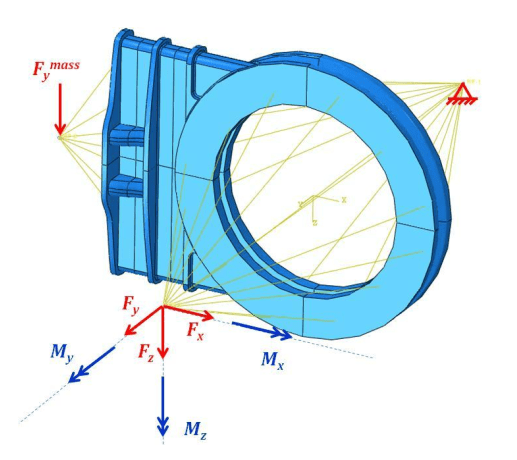
Hello everyone, I have questions about elastoplastic analysis in accordance with ASME VIII div.2. I want to check the valve body for possible types of failures: global failure and local failure in accordance with paragraphs 5.2.4 and 5.3.3 of the regulations.
I read the article PVP2017-65114, where the valve was calculated according to the same criteria.
In this article, the loads on the valve body are given in the form of pressure, external forces and moments without taking into account the flange tension example.
Therefore, there are several questions:
1) To what extent is it appropriate to ignore the precondition from fastener tightening during assembly, such as a spiral wound or RTJ gasket?
2) Factorized loads (with coefficients 2.4 and 1.7) take into account the pre-stress state from fastener tightening or is it still necessary to introduce counter flanges and use contact interaction with the pre-stress state? It is logical to assume that, given the preload, collapse will occur earlier.
3) If, for example, the mating flanges are not modeled, and the loads from the preliminary stress state are applied to the body (tightening force in the first step), in the second step, the reactions of the gaskets and all other loads (pressure, forces and moments from the pipeline).
Do the gasket reactions also need to be multiplied by the factors (2.4 and 1.7)?
4) In the same article, the load causing plastic collapse is obtained using the limit load method, why can't elastoplastic analysis also be used for this? Or ultimate load as a more conservative method in this case?
The task is a test for understanding the rules, thank you.