I have been working on a spreadsheet to help design footing sizes for PEMB's and I have come across an issue when the building columns are not at slab level. The company I work for uses hairpins to resist the kickout thrusts from the mainframes, but I am not quite sure how this works when the frames are up 2' for instance. My thinking is to make the pier strong enough that it can transfer the total horizontal thrust into the hairpins. I am also thinking that the rotation occurs about the point where the hairpin meets the slab. I have attached a sketch of the situation I am talking about with a circle around the point where I think rotation occurs. This is the point I am summing moments about in order to find the soil pressure.
I would love to hear if anyone has experience doing this and what the approach you took was or if there were any design guides that you found useful.
Thanks!
I would love to hear if anyone has experience doing this and what the approach you took was or if there were any design guides that you found useful.
Thanks!
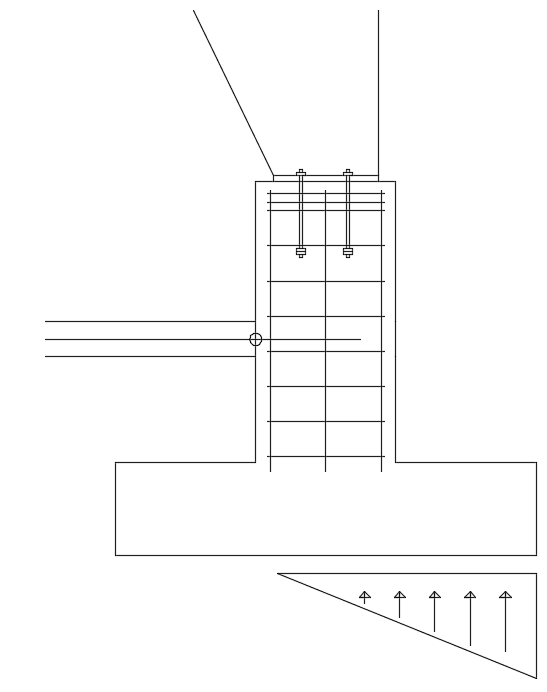