jdgengineer
Structural
- Dec 1, 2011
- 747
Wondering if any of you have designed relatively small elevated driveways connecting the street to a residence on a steep slope. I am looking at a project that may involve constructing one of these and I'm not sure I have run across it before so I thought I would get some input. The bridge is located over a steep hillside but I believe we should be able to support it along it's length (likely with drilled piers). In the neighborhood (constructed mostly in the 70s I believe) these appear to be wood framing with a thin slab poured on top. See below for some pictures.
It seems to me an elevated structural slab supported on concrete piers would be a good approach, but figured I would check in to see what else has been done. We do not have snow loads, but do have heavy seismic loads. I'm a bit concerned about a hard link from the street to the house with the bridge. Seems like we may want to get an expansion joint on one side.
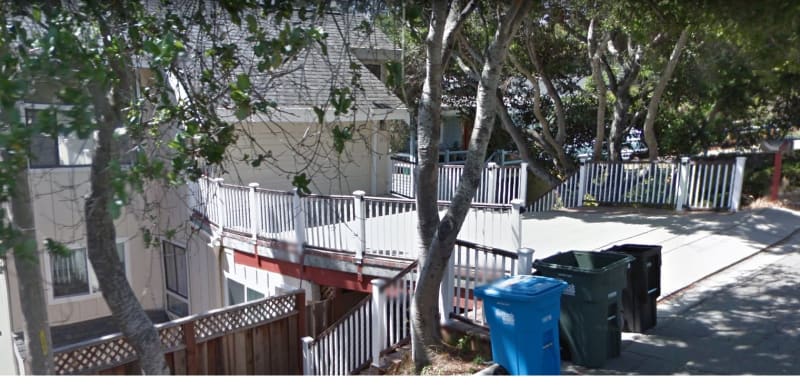
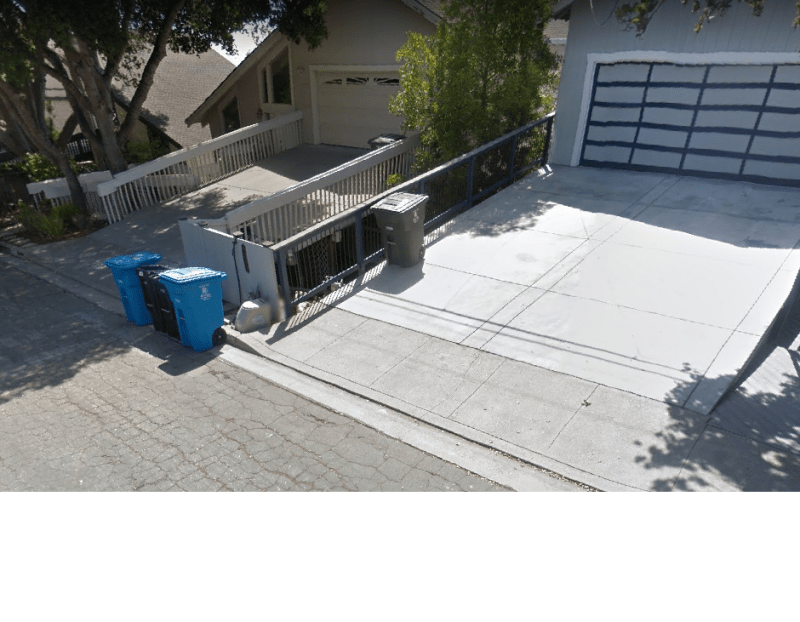
It seems to me an elevated structural slab supported on concrete piers would be a good approach, but figured I would check in to see what else has been done. We do not have snow loads, but do have heavy seismic loads. I'm a bit concerned about a hard link from the street to the house with the bridge. Seems like we may want to get an expansion joint on one side.