Gardenfence
Mechanical
- Jul 29, 2024
- 7
Hi,
I want to reduce a thin cylidrical shell model to a points along the centreline such that an equivalent beam model is formed with only bending modes. I am working in ABAQUS.
I have made a shell model, it has a non-circular cross section, uniform along length:
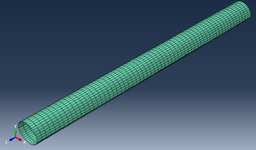
This model is partitioned into 60 equal sections, with a node posisitioned at the centre of each section (centre of mass). I have then applied a structural distributing coupling constraint on each centre node to the surrounding shell structure section.
Then using a Guyan reduction I have reduced the stiffness matrix to the centre nodes of the shell (centre nodes selected as masters). The reduced model has 360 DOF.
For the mass matrix I have used the Guyan transformation matrix and reduced the full mass matrix, and also I have also used lumped masses at on the nodes with the mass properties of each section obtained in ABAQUS.
With the approach of reducing the full mass matrix, I do get the bending modes of the structure, however, I also get loads of other modes corrosponding to the centreline motion the shell modes that I was hoping was going to be removed in the reduction.
Using lumped masses gives a worse result, where none of the modes makes sense and are confusing. There doesnt appear to be any bending modes in the reduced model following this approach.
Am I approaching this the wrong way? is there a better way to approach the reduction such that there are only bending modes remaining?
Any help would be appreciated!
I want to reduce a thin cylidrical shell model to a points along the centreline such that an equivalent beam model is formed with only bending modes. I am working in ABAQUS.
I have made a shell model, it has a non-circular cross section, uniform along length:
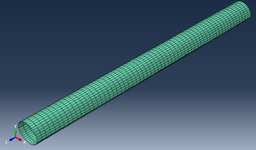
This model is partitioned into 60 equal sections, with a node posisitioned at the centre of each section (centre of mass). I have then applied a structural distributing coupling constraint on each centre node to the surrounding shell structure section.
Then using a Guyan reduction I have reduced the stiffness matrix to the centre nodes of the shell (centre nodes selected as masters). The reduced model has 360 DOF.
For the mass matrix I have used the Guyan transformation matrix and reduced the full mass matrix, and also I have also used lumped masses at on the nodes with the mass properties of each section obtained in ABAQUS.
With the approach of reducing the full mass matrix, I do get the bending modes of the structure, however, I also get loads of other modes corrosponding to the centreline motion the shell modes that I was hoping was going to be removed in the reduction.
Using lumped masses gives a worse result, where none of the modes makes sense and are confusing. There doesnt appear to be any bending modes in the reduced model following this approach.
Am I approaching this the wrong way? is there a better way to approach the reduction such that there are only bending modes remaining?
Any help would be appreciated!