MegaStructures
Structural
I have a error that is driving me mad. I have created a model of an HSS connection using shell mesh. For some reason where two HSS meet eachother I am getting an error that
1) Mesh is distorted
2) There are zero area elements
No matter how much I refine the mesh the problem doesn't go away. What could be causing this? The red element in the below picture is the only element with the second warning and the Abaqus model is attached.
“The most successful people in life are the ones who ask questions. They’re always learning. They’re always growing. They’re always pushing.” Robert Kiyosaki
1) Mesh is distorted
2) There are zero area elements
No matter how much I refine the mesh the problem doesn't go away. What could be causing this? The red element in the below picture is the only element with the second warning and the Abaqus model is attached.
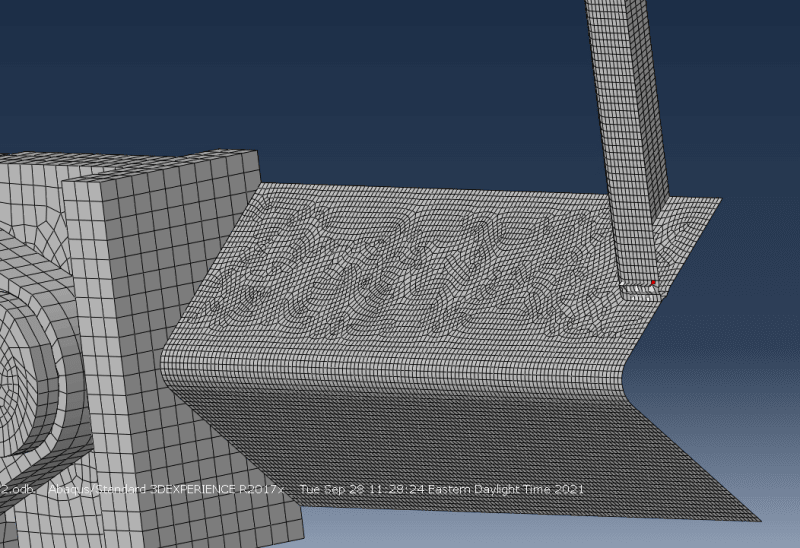
“The most successful people in life are the ones who ask questions. They’re always learning. They’re always growing. They’re always pushing.” Robert Kiyosaki