Burunduk
Mechanical
- May 2, 2019
- 2,563
Fig. 2-22 in ASME Y14.5 shows a crescent-shaped tolerance zone that starts and ends tangent to 2 straight outlines of features that the radius connects.
When evaluating if an actual produced radius is within tolerance, what sets those 2 straight lines/planes? The actual produced "flat" surfaces will have flatness error, so how one aligns the theoretical tolerance zone with the actual part?
Consider that there is a potential deviation from the tolerance zone approximately around the marked area. The way the tolerance zone is overlayed on the part may be an important factor for whether to accept or reject.
When evaluating if an actual produced radius is within tolerance, what sets those 2 straight lines/planes? The actual produced "flat" surfaces will have flatness error, so how one aligns the theoretical tolerance zone with the actual part?
Consider that there is a potential deviation from the tolerance zone approximately around the marked area. The way the tolerance zone is overlayed on the part may be an important factor for whether to accept or reject.
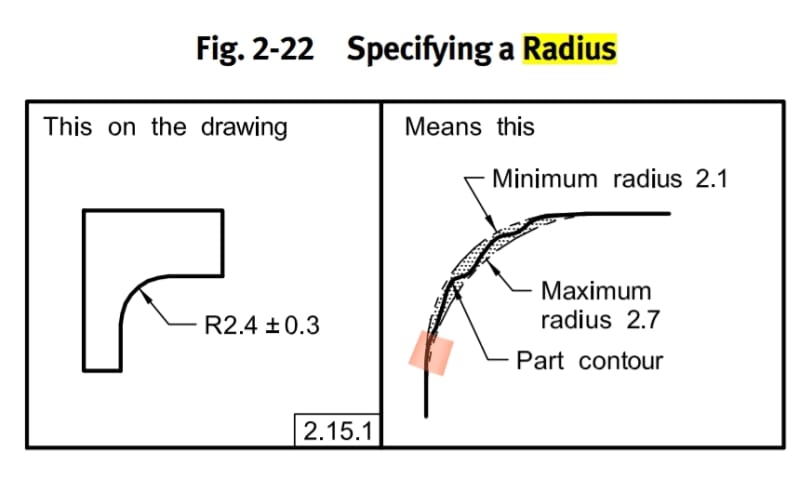