mfstructural
Structural
- Feb 1, 2009
- 230
I have a project where my client has a half full basement and half crawlspace in his home. He wants to expand the full basement to have more space. I have existing plans that show the full height of the crawl space foundation walls as 4' and full height of basement walls as 8.5'. I'm planning to have them excavate the soil in 4' segments to cut off the inner portion of the strip footing even with the interior face of the existing fdn wall and dowel into the underside of the existing wall. The dowels will have to be able to withstand the hydrostatic forces on the wall, particularly because of the construction joint in the concrete.
The other issue is the interior columns, pictured below. shoring will be required to support the existing steel beams (and wood joists). Once shoring is installed the existing columns can be removed, soil excavated, new footings poured. Longer steel columns will then be installed.
Any thoughts on other things I should be considering? I've attached a rough sketch of what I'm thinking without dowels.
The other issue is the interior columns, pictured below. shoring will be required to support the existing steel beams (and wood joists). Once shoring is installed the existing columns can be removed, soil excavated, new footings poured. Longer steel columns will then be installed.
Any thoughts on other things I should be considering? I've attached a rough sketch of what I'm thinking without dowels.
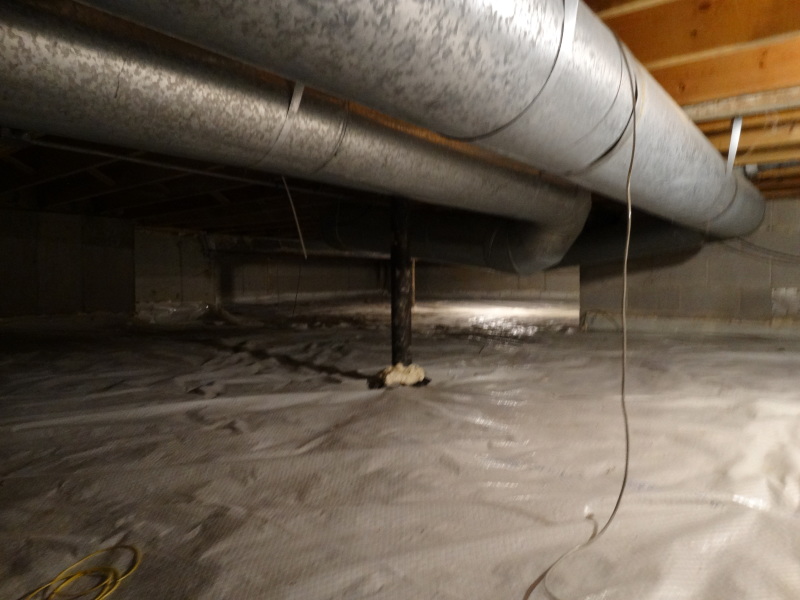
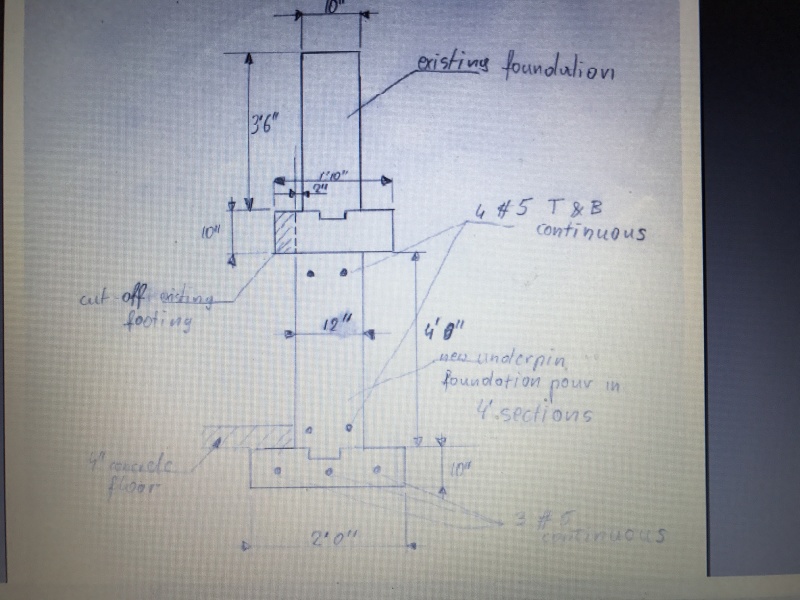