Usman3301
Civil/Environmental
- Jul 11, 2019
- 48
Hi there,
I am a junior engineer, currently working on textile mill project and facing an issue, which I haven't been able to resolve for past 3-4 days.
Story heights for textile mill have been shown in images. On Gridlines 17,18,19 and 20, an AC station will be placed and its subsequent loads have been applied on this model. At story - 1, SOG will be placed and therefore restraints in x,y direction have been applied in model.
When analysis is run and concrete frame design as well, software provides excessive reinforcement at zero points of column against governing gravity load combo. Initially, I thought this maybe due to slenderness effects, but I have checked manually that slenderness doesn't control here. (column size is 21"x21"). Secondly, I thought this might be due to lateral load effects (site is located in zone 2B (Intermediate moment frame)) but gravity load combo ruled out this possibility as well. Also, I have designed column manually against given moments, 24"x24" cross-section will be okay but ETABS model says otherwise. I have run out of ideas and I have to submit design calcs to senior engineer by tomorrow. Kindly help me out in this and assist me in understanding why I am getting these values.
3D MODEL:
AXIAL FORCES IN COLUMNS
GOVERNING MOMENTS IN COLUMNS
COLUMN REINFORCEMENT (unit - in^2)
COLUMN DESIGN DETAILS (GRID F-18)
I am a junior engineer, currently working on textile mill project and facing an issue, which I haven't been able to resolve for past 3-4 days.
Story heights for textile mill have been shown in images. On Gridlines 17,18,19 and 20, an AC station will be placed and its subsequent loads have been applied on this model. At story - 1, SOG will be placed and therefore restraints in x,y direction have been applied in model.
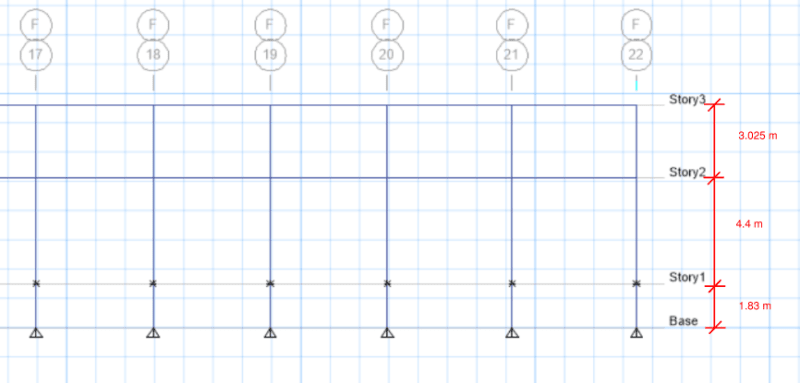
When analysis is run and concrete frame design as well, software provides excessive reinforcement at zero points of column against governing gravity load combo. Initially, I thought this maybe due to slenderness effects, but I have checked manually that slenderness doesn't control here. (column size is 21"x21"). Secondly, I thought this might be due to lateral load effects (site is located in zone 2B (Intermediate moment frame)) but gravity load combo ruled out this possibility as well. Also, I have designed column manually against given moments, 24"x24" cross-section will be okay but ETABS model says otherwise. I have run out of ideas and I have to submit design calcs to senior engineer by tomorrow. Kindly help me out in this and assist me in understanding why I am getting these values.
3D MODEL:
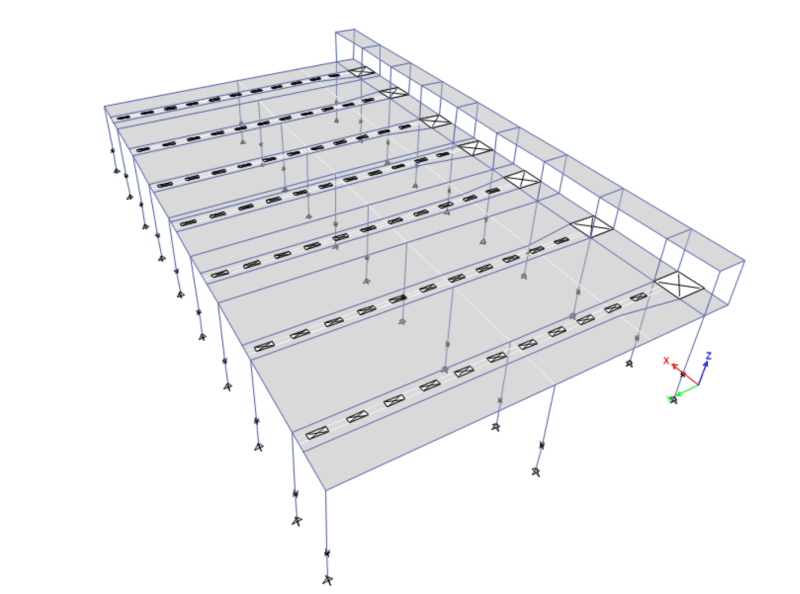
AXIAL FORCES IN COLUMNS
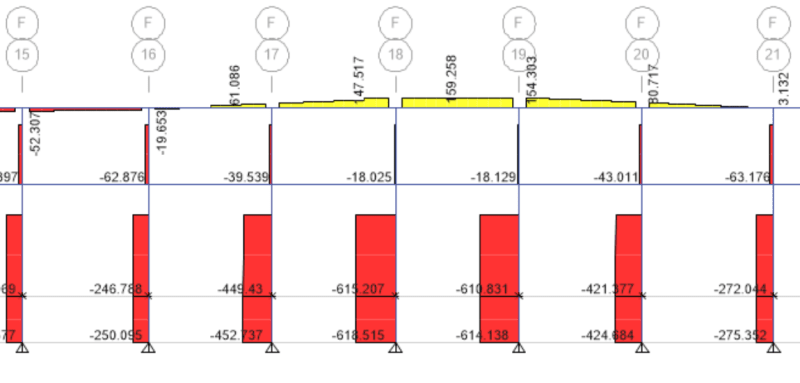
GOVERNING MOMENTS IN COLUMNS
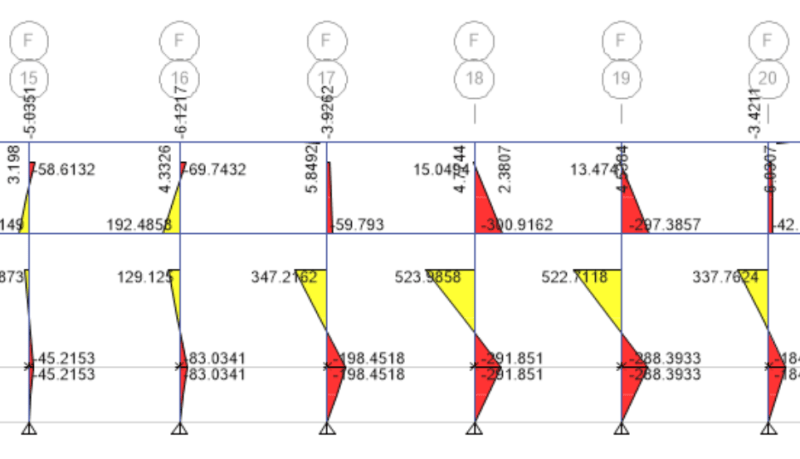
COLUMN REINFORCEMENT (unit - in^2)
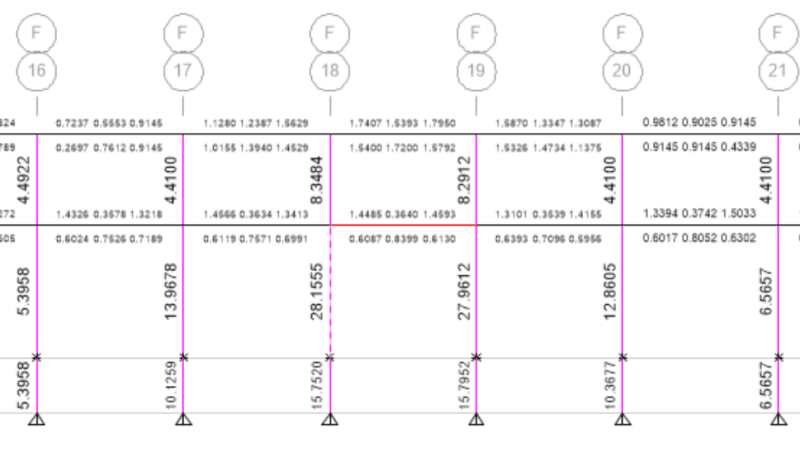
COLUMN DESIGN DETAILS (GRID F-18)
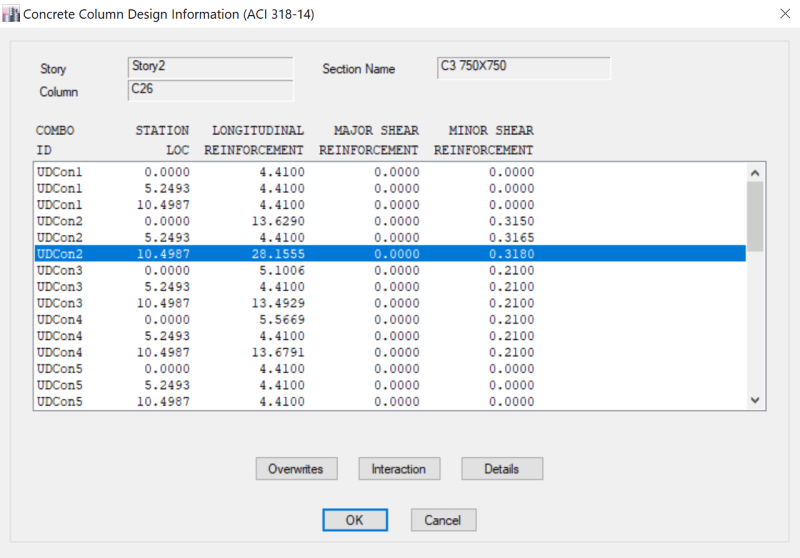
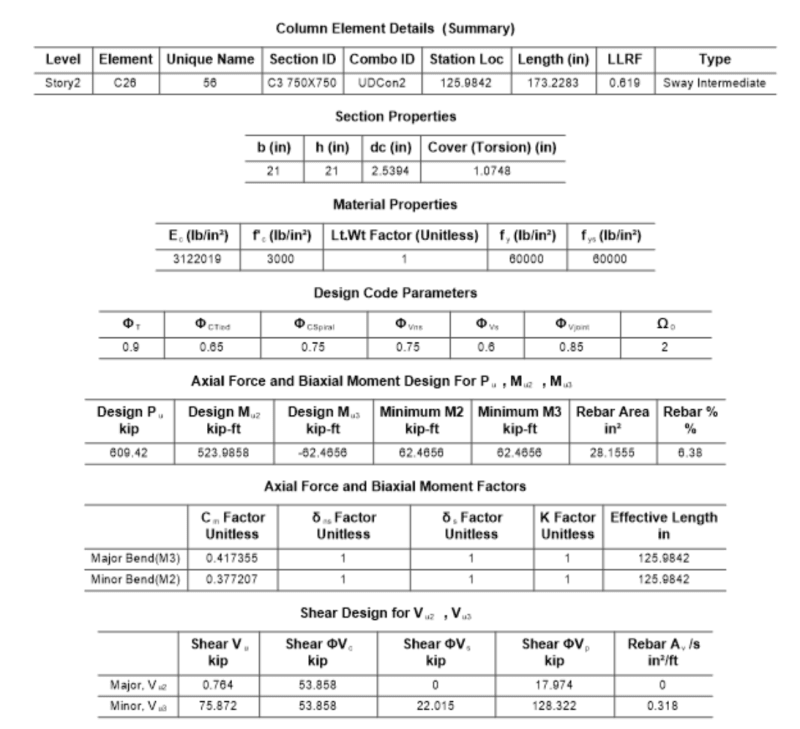