I have a 2D lattice structure, where each strut consists of multiple beam elements (B22). The lattice is sandwiched between two plates, that compress the lattice. I run the simulation on Abaqus Explicit and apply General Contact. However, already in the very first computation, before the lattice is much deformed, I get excessively distorted elements (see pic below -- the beams are supposed to form a straight line between the nodes).
When I run the simulation with contact between the lattice and plates only, it works perfectly, but (obv) the beam elements are ghosting each other.
When I run the exact same simulation (with General Contact) in 3D, using B32 elements and BC to constrain the out of plane movement, it also works perfectly, but is much slower.
Is there a known bug or workaround for this? Thanks!
When I run the simulation with contact between the lattice and plates only, it works perfectly, but (obv) the beam elements are ghosting each other.
When I run the exact same simulation (with General Contact) in 3D, using B32 elements and BC to constrain the out of plane movement, it also works perfectly, but is much slower.
Is there a known bug or workaround for this? Thanks!
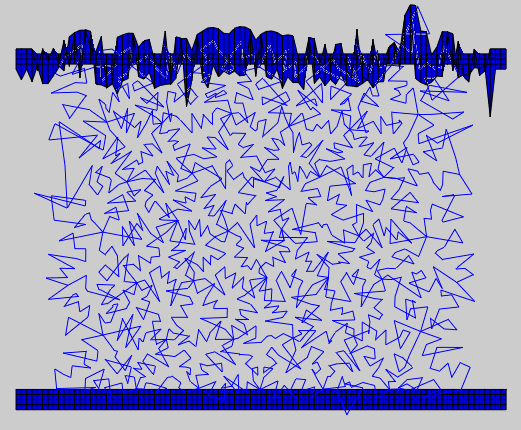