Hi all,
Question for you (also posted in the structural subforum) - We installed an alternating tread stair system into a potable water reservoir two years ago. The railing on the platforms was spec'd as Type 316L SS while the alternating tread stairs were fabricated from Type 304 SS. As you can see in the photo below, both of these components are experience significant signs of rust/corrosion - especially considering they're only two years old!
Just wondering if any of you have experience in the fabrication of stainless steel components of similar size/nature. Our theory is that the materials were improperly handled and cross-contaminated with carbon steel (eg. cutting/grinding with equipment used on carbon steel, lifting with steel chains, skid steer forks, etc.). The worst areas are definitely where the SS pipes have been manipulated (at the railing corners/welds for example) which supports our theory.
I'm curious if any of you have any experience with passivation of stainless steel after fabrication? We spoke briefly with a local fabricator who suggested that for members such as these, they would have re-passivated the members by spraying them with nitric acid after fabrication... Is this standard industry practice? Ever hear of anyone doing this? Is it called up in any ASTMs or other codes?
If you can share your experience with stainless steel fabrication (specifically worked members such as these) and what the industry norms are, that would be appreciated!
The other theory is simply that SS does not fare well against high-chlorine environments - being a potable water reservoir, there is a fair amount of chlorine in the air. That said, we are well below the chlorine levels that are documented to cause a concern for SS.
Cheers,
Question for you (also posted in the structural subforum) - We installed an alternating tread stair system into a potable water reservoir two years ago. The railing on the platforms was spec'd as Type 316L SS while the alternating tread stairs were fabricated from Type 304 SS. As you can see in the photo below, both of these components are experience significant signs of rust/corrosion - especially considering they're only two years old!
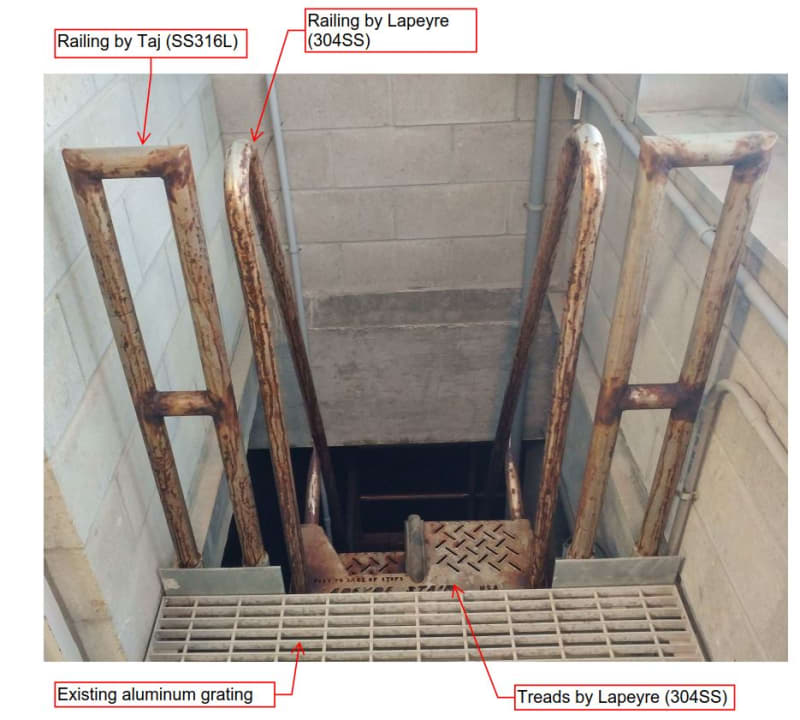
Just wondering if any of you have experience in the fabrication of stainless steel components of similar size/nature. Our theory is that the materials were improperly handled and cross-contaminated with carbon steel (eg. cutting/grinding with equipment used on carbon steel, lifting with steel chains, skid steer forks, etc.). The worst areas are definitely where the SS pipes have been manipulated (at the railing corners/welds for example) which supports our theory.
I'm curious if any of you have any experience with passivation of stainless steel after fabrication? We spoke briefly with a local fabricator who suggested that for members such as these, they would have re-passivated the members by spraying them with nitric acid after fabrication... Is this standard industry practice? Ever hear of anyone doing this? Is it called up in any ASTMs or other codes?
If you can share your experience with stainless steel fabrication (specifically worked members such as these) and what the industry norms are, that would be appreciated!
The other theory is simply that SS does not fare well against high-chlorine environments - being a potable water reservoir, there is a fair amount of chlorine in the air. That said, we are well below the chlorine levels that are documented to cause a concern for SS.
Cheers,