nondimensional
Mechanical
Does anyone have any experience in designing/sizing the control rods for the expansion joints indicated in the picture below? I have zero thrust blocks/anchors in the piping system except where the pipe emerges from the ground on the suction header and goes back below ground on discharge header (the buried portion is considered anchored). All the supports I have are sliding supports. The expansion joints are required to be able to pull the pump out of service and reinstall. Assume a slight (~1/8 inch) misalignment that needs to be compensated by the joint. NO EXPANSION is preferred whatsoever - to avoid any loads on pump nozzles. Pumps are installed on solid concrete foundation, anchored down to the foundation.
4000 gpm each pump
16-inch pump suction (15.25 ID)
14-inch pump disch (13.25 ID)
24-inch suction header
30-inch discharge header
Ps = 20 psig
Pd = 120 psig
Pdiff = 100 psig
4000 gpm each pump
16-inch pump suction (15.25 ID)
14-inch pump disch (13.25 ID)
24-inch suction header
30-inch discharge header
Ps = 20 psig
Pd = 120 psig
Pdiff = 100 psig
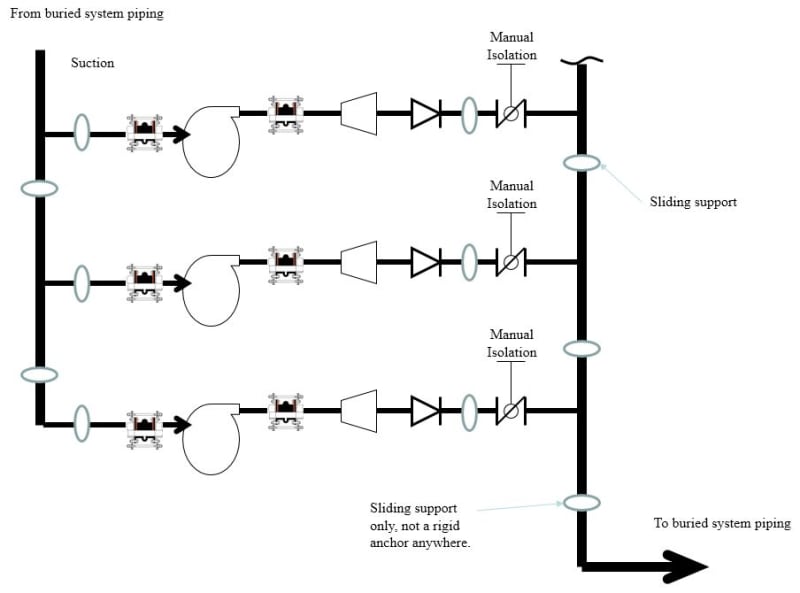