elinah34
Mechanical
- Aug 19, 2014
- 149
Hello,
I have a question about a thread which exists in a bonded joint.
I am adding a simplified picture of such a joint, that we have some issues with:
Please pay attention that the thread goes a little bit over the second lower bonded Ultem part.
After manufacturing this joint (Including inserting the Tangles Helicoil, a special Helicoil for Plastics which doesn't require exerting any force for inserting it to its place, but only threading it to its place) everything was fine, and there was no evidence of separation in the interface of both Ultem parts while examining it visually and ultrasonically.
After tightening the bolt exactly as described in the picture above, exerting 10 Lb*Inch, we found out that it caused a separation between the 2 Ultem parts (the Adhesive didn't succeed holding them together).
We can't understand the root cause of this failure because the tightening force should attach the parts to each other.
We thought about a potential failure mechanism, but we aren't sure about it – the external load is never uniformly distributed along the thread's teeth (see an example below), and maybe this may cause a relative movement?
I have a question about a thread which exists in a bonded joint.
I am adding a simplified picture of such a joint, that we have some issues with:
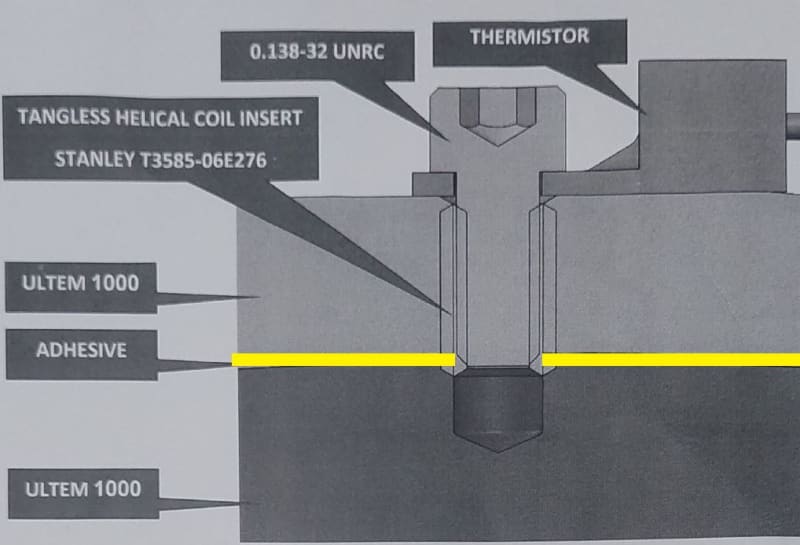
Please pay attention that the thread goes a little bit over the second lower bonded Ultem part.
After manufacturing this joint (Including inserting the Tangles Helicoil, a special Helicoil for Plastics which doesn't require exerting any force for inserting it to its place, but only threading it to its place) everything was fine, and there was no evidence of separation in the interface of both Ultem parts while examining it visually and ultrasonically.
After tightening the bolt exactly as described in the picture above, exerting 10 Lb*Inch, we found out that it caused a separation between the 2 Ultem parts (the Adhesive didn't succeed holding them together).
We can't understand the root cause of this failure because the tightening force should attach the parts to each other.
We thought about a potential failure mechanism, but we aren't sure about it – the external load is never uniformly distributed along the thread's teeth (see an example below), and maybe this may cause a relative movement?
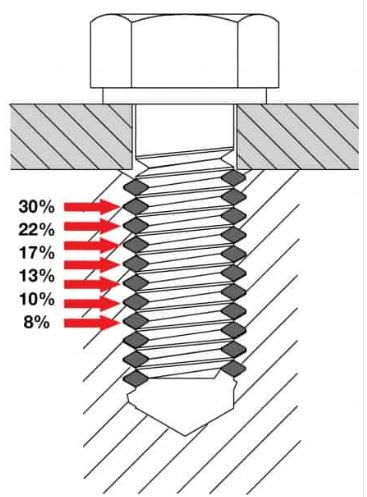