Lee.Conti
Automotive
- Nov 8, 2019
- 87
Hi All,
I am trying to compare using FEA results to calculate the bolt forces with the hand calculation from Shigley example... but I can't match it... I extract the forces and also moment... but I am not sure if the FEA results are correct although summation of forces are matching to applied force...
Anyone can tell what I miss out in the FEA?
I am trying to compare using FEA results to calculate the bolt forces with the hand calculation from Shigley example... but I can't match it... I extract the forces and also moment... but I am not sure if the FEA results are correct although summation of forces are matching to applied force...
Anyone can tell what I miss out in the FEA?
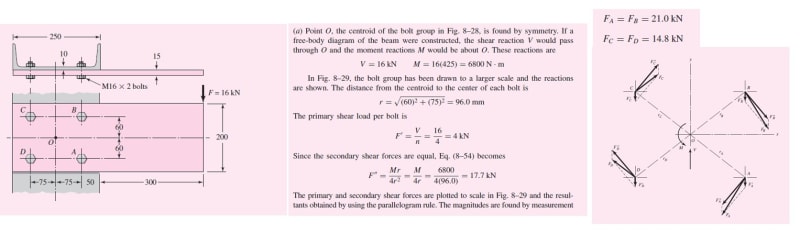
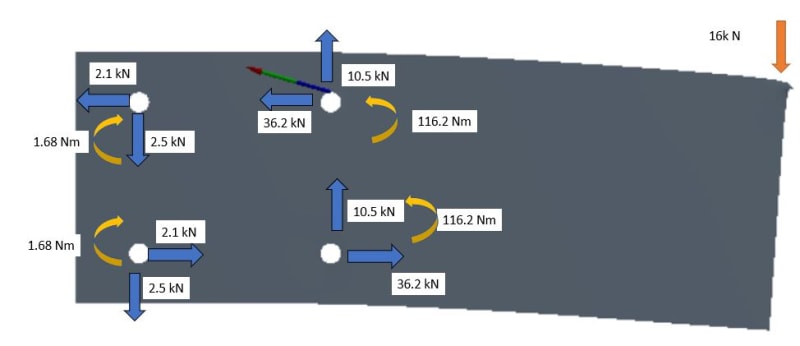