Hi!
I'm in need of some assistance, and hopefully someone here can help me
I have an aluminum U chanel that where a cladding will be fixed. This cladding will transmit forces according to the scheme below.
This forces will tranlate on a bending moment according to the yy axis on the aluminum chanel and steel bar.
Can someone help me on how to properly design the spacing and specifications of the bolt for a specific Bending moment on yy?
How can I calculate the shear forces?
I'm in need of some assistance, and hopefully someone here can help me

I have an aluminum U chanel that where a cladding will be fixed. This cladding will transmit forces according to the scheme below.
This forces will tranlate on a bending moment according to the yy axis on the aluminum chanel and steel bar.
Can someone help me on how to properly design the spacing and specifications of the bolt for a specific Bending moment on yy?
How can I calculate the shear forces?
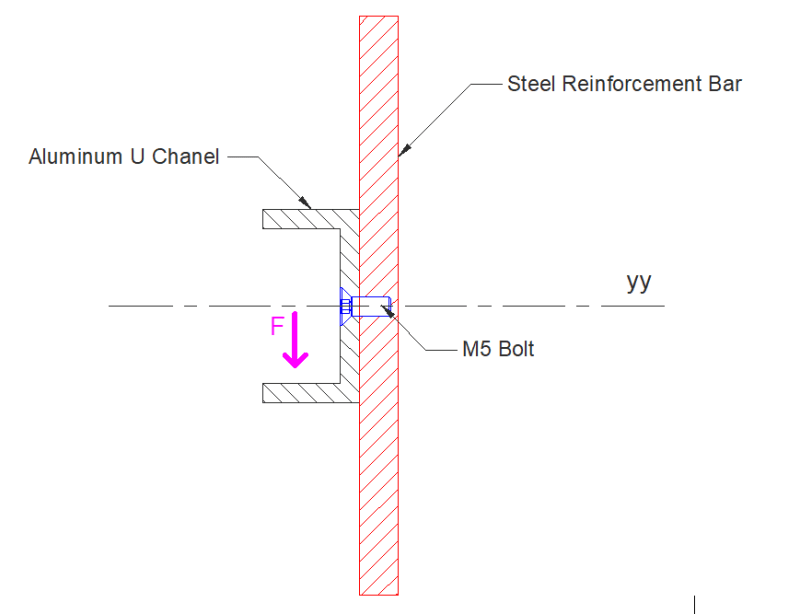