fem.fan
Mechanical
- Jun 7, 2021
- 33
hi, every time i model a nozzle connection i come across the same problem: " how much shell to model". i have tried many options but none of them quite satisfies me.
if i model the whole circumference of the sheell with solid elements, it takes a lot of elements and thus, a great computational cost.
i tried modeling just a part of the circumference applying symmetry conditions, say 1/4 or 1/2 of shell, but it doesn´t seem right since the symmetry is not real.
my last and final approach was to model a great part of the shell with shell elements, the nozzle and its surroundings with solid elements and then coupling them with multipoint constraints. this was a great solution for elastic material problems, but when using elastoplastic materials as per ASME - VIII div. 2 part 5 the rigid connectiones provoked a convergence issue due to highly concentrated unrealistic plastic srtains.
these images illustrate each option.
full circumference with solids
1/4 of circumference with solids
shell to solid coupling
highly concentrated plastic strains
can anyone give some insight on the matter?
thanks in advance.
if i model the whole circumference of the sheell with solid elements, it takes a lot of elements and thus, a great computational cost.
i tried modeling just a part of the circumference applying symmetry conditions, say 1/4 or 1/2 of shell, but it doesn´t seem right since the symmetry is not real.
my last and final approach was to model a great part of the shell with shell elements, the nozzle and its surroundings with solid elements and then coupling them with multipoint constraints. this was a great solution for elastic material problems, but when using elastoplastic materials as per ASME - VIII div. 2 part 5 the rigid connectiones provoked a convergence issue due to highly concentrated unrealistic plastic srtains.
these images illustrate each option.
full circumference with solids
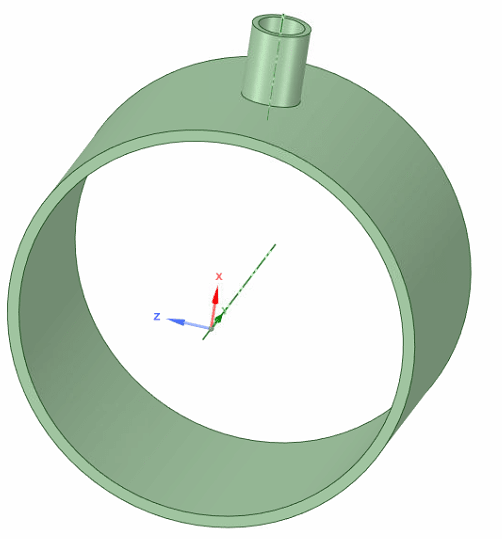
1/4 of circumference with solids
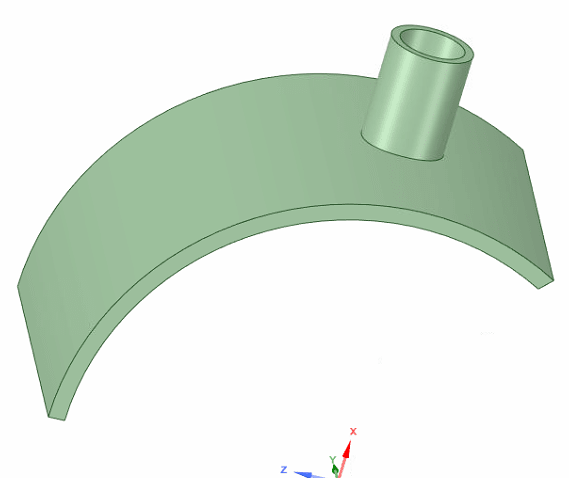
shell to solid coupling
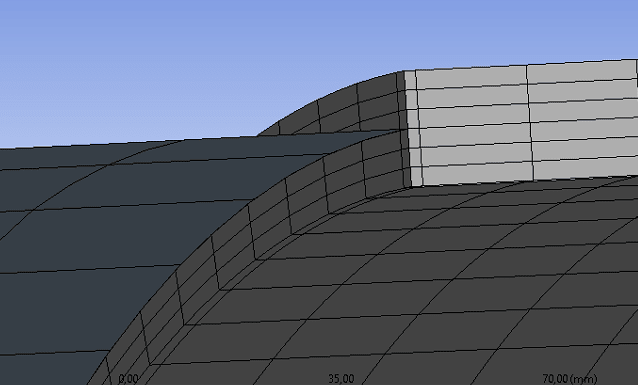
highly concentrated plastic strains
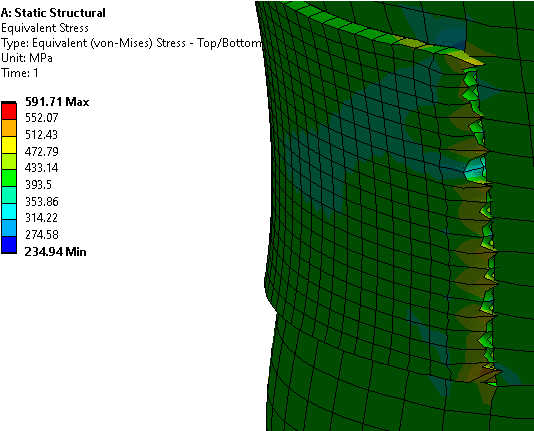
can anyone give some insight on the matter?
thanks in advance.