_charlie.gee
Student
Hi, I'm doing my final year project on FEA and using image decomposition programs. I'm modelling a rocket nozzle, and have done 1/4 of it with axissymmetric loading conditions with a pressure acting outwards. I believe it's loaded and constrained correctly however I'm having issues with convergence and mesh refinement. I'm looking for the max Von Mises Stress in the whole model which is at the top of the model (throat) on the outside edge, and started with mesh refinement, making a small region at the top where I'm refining the mesh. As you can see from the attached pics my residuals between refinement for max and min stress are all over the place and I'm just not sure where I'm going wrong or what to do. There's no hint of convergence and I cant progress with my project, been at a standstill for the past 2 weeks as I need to choose a single piece of data to talk about at length for the next writeup.
Any help clearing this up would be greatly appreciated maybe it's correct but I'm just failing to interpret the results correctly?
Thanks
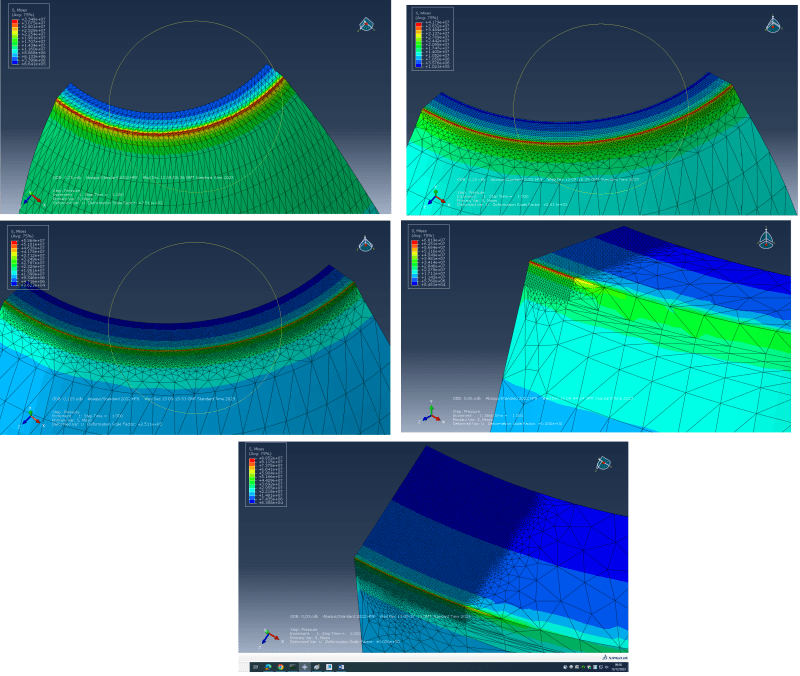
Any help clearing this up would be greatly appreciated maybe it's correct but I'm just failing to interpret the results correctly?
Thanks