FEA_SJ
Mechanical
- Dec 19, 2019
- 5
Hi,
I am trying to conduct a load analysis for a 3 Bolt Clamp. I would like to get your thoughts on how to set up my model for analysis. The way I have it set up is: The top bolt hole is fixed and the load is on the pipe at the 60-degree bearing surface. The pipe is set to be rigid. There is no penetration contact between the pipe and the clamp. In this case, the pipe size is 3". The load is 1000 lbs @ 1000deg F. The max allowable stress as per MSS SP58 @ 1000 deg is 8KSI for A3875. The stock size is 1/4" X 1-1/4". Please if anyone could verify this setup for accuracy or have any other ideas on how to improvise on it, that would be great.
Based on my set up the stress value is coming out to be way above the allowable. This should not be the case as we have been using these clamps in the field for a very long time without any issues.
I am trying to conduct a load analysis for a 3 Bolt Clamp. I would like to get your thoughts on how to set up my model for analysis. The way I have it set up is: The top bolt hole is fixed and the load is on the pipe at the 60-degree bearing surface. The pipe is set to be rigid. There is no penetration contact between the pipe and the clamp. In this case, the pipe size is 3". The load is 1000 lbs @ 1000deg F. The max allowable stress as per MSS SP58 @ 1000 deg is 8KSI for A3875. The stock size is 1/4" X 1-1/4". Please if anyone could verify this setup for accuracy or have any other ideas on how to improvise on it, that would be great.
Based on my set up the stress value is coming out to be way above the allowable. This should not be the case as we have been using these clamps in the field for a very long time without any issues.
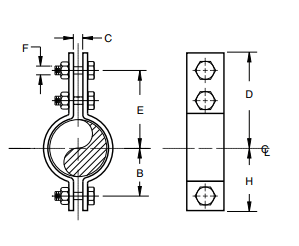
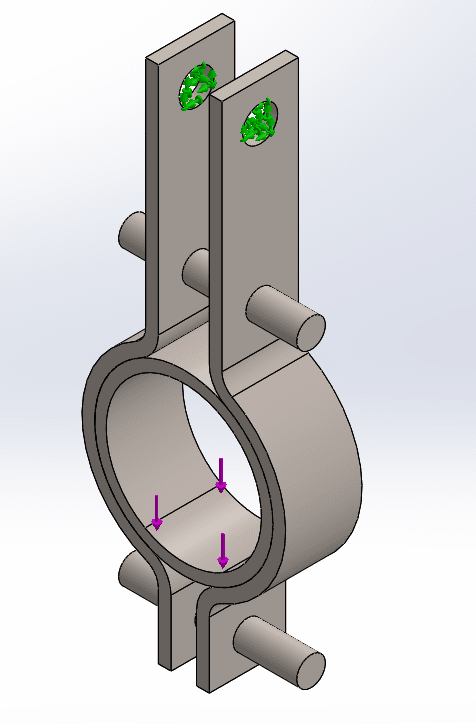