Hi,
Pretty fundamental/basic question, but I'm not finding a reference for the "standard" or best practice statement. I consider it to be double dimensioning if the quantity and centerlines are used simultaneously. Referring the the crude sketch below, the usage of centerlines OR quantity callout is permissible, but not both. What's the 14.X or best practice statement stating such?
Thanks,
Pretty fundamental/basic question, but I'm not finding a reference for the "standard" or best practice statement. I consider it to be double dimensioning if the quantity and centerlines are used simultaneously. Referring the the crude sketch below, the usage of centerlines OR quantity callout is permissible, but not both. What's the 14.X or best practice statement stating such?
Thanks,
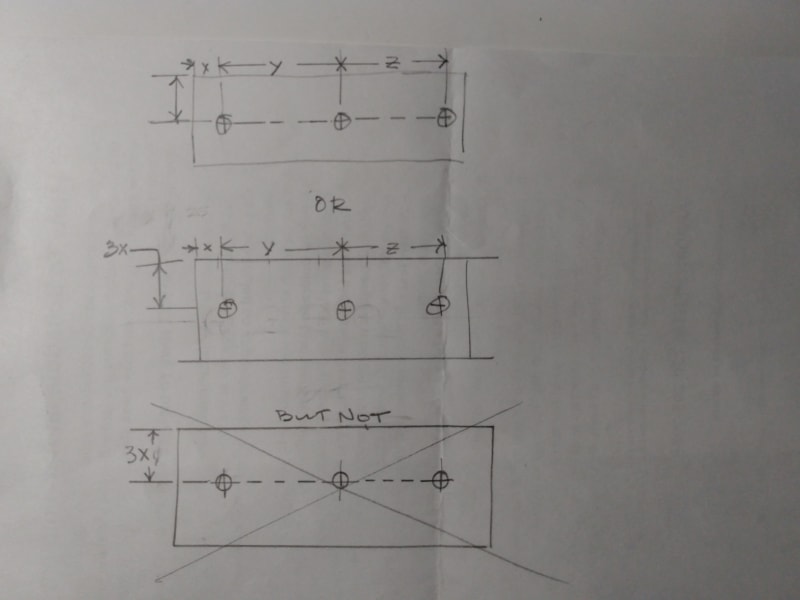