a50860
Aerospace
- Jan 28, 2012
- 10
Hello, I need to provide a design to field weld a splice connection between 2 box truss beams that have plated ends. We normally bolt them together, however, the plate hole patterns aren't aligning. I'd like to weld the plates together and was hoping for some feedback on my plan. Any feedback would be greatly appreciated!
geometry:
- box truss beam with plated ends. the beam is split into 3 equal parts with splices at 1/3rds.
loading:
- vertical cyclical loading with a known dead weight
- horizontal wind load per ASEC7
- normal loading conditions with the bottom of the beam in tension and top in compression. +/- for the wind plane.
plan:
I'd like to specify SMAW with AWS D1.1-2020 detail BC-P2 since T1 allows unlimited depth. however, I don't think I really have a butt weld here, but I can't find a good match for welding edges of plates together. can I consider this a large butt weld and use detail B-P3?
issues:
- D1.1 4.18.1 one-sided groove welds is prohibited for cyclical loading
I'm wondering if anyone knows a better prequalified weld detail to use if I plan to add weld to portions of all sides of my plate connection?
Thanks for taking a look!
--
Mitch
geometry:
- box truss beam with plated ends. the beam is split into 3 equal parts with splices at 1/3rds.
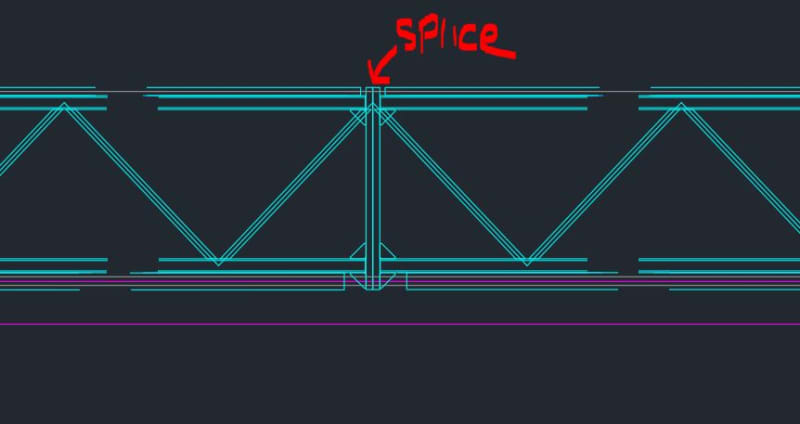
loading:
- vertical cyclical loading with a known dead weight
- horizontal wind load per ASEC7
- normal loading conditions with the bottom of the beam in tension and top in compression. +/- for the wind plane.
plan:
I'd like to specify SMAW with AWS D1.1-2020 detail BC-P2 since T1 allows unlimited depth. however, I don't think I really have a butt weld here, but I can't find a good match for welding edges of plates together. can I consider this a large butt weld and use detail B-P3?
issues:
- D1.1 4.18.1 one-sided groove welds is prohibited for cyclical loading
I'm wondering if anyone knows a better prequalified weld detail to use if I plan to add weld to portions of all sides of my plate connection?
Thanks for taking a look!
--
Mitch