Hi, I have a Piping line list with various design conditions. Say, For carbon steel material 150#, 10"pipe, there are various pressure and temperatures. Should I calculate the pipe wall thk for each condition as per ASME B31.3. Or is there a shorter way? How to arrive at the most most critical service and generalise it to the entire selection? Pls have a look at the file attached for reference
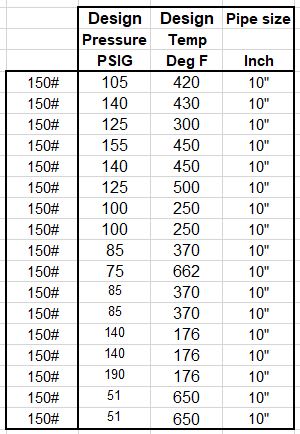