eli28
Aerospace
- Oct 20, 2019
- 109
Does anyone has an idea how can I find the optimum shape of the slot in the mechanism described schematically in the attached picture?
I can say that we probably want the lower slot surface normals to coincide with the vertical axis of movement, but I am not sure how to analytically or technically plotting it (maybe in CAD?)
I can say that we probably want the lower slot surface normals to coincide with the vertical axis of movement, but I am not sure how to analytically or technically plotting it (maybe in CAD?)
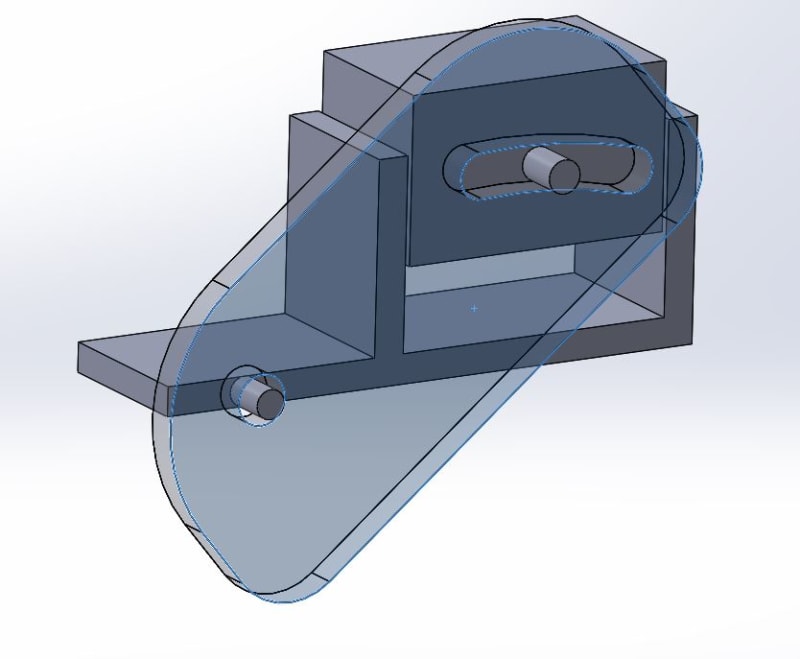