VFreshEngineer
Mechanical
Hello everyone, hope You all are staying safe in these challenging times.
I'm designing fin-tube heat exchanger (water-air). I have all the calculations needed, heat exchanger is manufactured & tested and works great, but as a curious person I'm still wondering about some theoretical aspects. I currently don't have any collegues in mechanical department, so I really appreciate any discussion on the subject. I'm still very fresh engineer, so correct me if I'm wrong anywhere along the way.
To visualize the case a little better, here is a simplified drawing of heat exchanger:
Knowing the coolant flow for the cooling loop and the size of the Inlet/Outlet coolant connections, we can find the velocity of fluid using: Q = V/t = A*v = (πd2v)/4
If coolant connections sizes are the same, in&out velocity of fluid will also be the same. (Flow in = Flow out = constant)
Questions:
1. What about the velocity of fluid inside the tubes? Will the flow inside single fin-tube be "Q/number of tubes"? (Q: system flow)
2. If (1) is the correct assumption, then more fin tubes inside heat exchanger = lower fluid velocity inside single fin-tube = larger cooling capacity, but higher outlet temperature of the coolant.
3. I'm calculating Reynolds Number by multiplying "Mass Flow unit Area" with fin-tube diameter and dividing the product with "Dynamic Exhaust Viscosity @ Mean Temperature". [Re=(G[sub]n[/sub]*d)/μE_Mean]. My superior says that Reynolds number should be below 12000, but he doesn't really know how to support this statement with scientific knowledge. Is there any way to establish the limits for Reynolds number? Or is there some kind of rule of thumb? I've only learned that for a flow inside a pipe to be laminar, the Reynolds number should be kept under 2000, but that's simplification I remember from uni.
4. Is there any critical velocity for the fluid flow? I remember I've read somewhere that it's usually kept under 3 m/s, as a rule of thumb. However, I don't know more. The only reason I can think of is that the force of moving fluid on the structure (walls) shouldn't exceed certain value.
Anyway, I think that's it for now. If any additional questions will pop in my head, I'll surely update.
I appreciate every single input. Thanks in advance!
I'm designing fin-tube heat exchanger (water-air). I have all the calculations needed, heat exchanger is manufactured & tested and works great, but as a curious person I'm still wondering about some theoretical aspects. I currently don't have any collegues in mechanical department, so I really appreciate any discussion on the subject. I'm still very fresh engineer, so correct me if I'm wrong anywhere along the way.
To visualize the case a little better, here is a simplified drawing of heat exchanger:
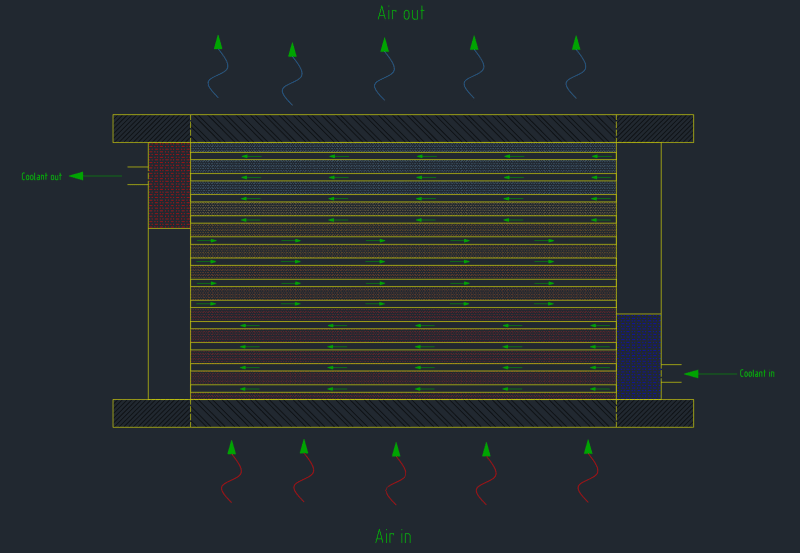
Knowing the coolant flow for the cooling loop and the size of the Inlet/Outlet coolant connections, we can find the velocity of fluid using: Q = V/t = A*v = (πd2v)/4
If coolant connections sizes are the same, in&out velocity of fluid will also be the same. (Flow in = Flow out = constant)
Questions:
1. What about the velocity of fluid inside the tubes? Will the flow inside single fin-tube be "Q/number of tubes"? (Q: system flow)
2. If (1) is the correct assumption, then more fin tubes inside heat exchanger = lower fluid velocity inside single fin-tube = larger cooling capacity, but higher outlet temperature of the coolant.
3. I'm calculating Reynolds Number by multiplying "Mass Flow unit Area" with fin-tube diameter and dividing the product with "Dynamic Exhaust Viscosity @ Mean Temperature". [Re=(G[sub]n[/sub]*d)/μE_Mean]. My superior says that Reynolds number should be below 12000, but he doesn't really know how to support this statement with scientific knowledge. Is there any way to establish the limits for Reynolds number? Or is there some kind of rule of thumb? I've only learned that for a flow inside a pipe to be laminar, the Reynolds number should be kept under 2000, but that's simplification I remember from uni.
4. Is there any critical velocity for the fluid flow? I remember I've read somewhere that it's usually kept under 3 m/s, as a rule of thumb. However, I don't know more. The only reason I can think of is that the force of moving fluid on the structure (walls) shouldn't exceed certain value.
Anyway, I think that's it for now. If any additional questions will pop in my head, I'll surely update.
I appreciate every single input. Thanks in advance!