paintballJim
Mechanical
- Dec 23, 2009
- 56
I am interested in the correct weld symbol for a flair-bevel weld where the weld is expected to be flush with the material when finished.
The question that has come up is if the throat dimension is needed if you indicate that the weld finish is flush. I have always added the weld size to my symbols but maybe that is not needed in this case? below I have added the dimension and a grind symbol, but if it is not necessary for the surface to be ground smooth is it acceptable to leave the dimension off and just expect the weld to be roughly flush to the material surface?
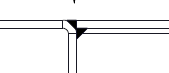
The question that has come up is if the throat dimension is needed if you indicate that the weld finish is flush. I have always added the weld size to my symbols but maybe that is not needed in this case? below I have added the dimension and a grind symbol, but if it is not necessary for the surface to be ground smooth is it acceptable to leave the dimension off and just expect the weld to be roughly flush to the material surface?
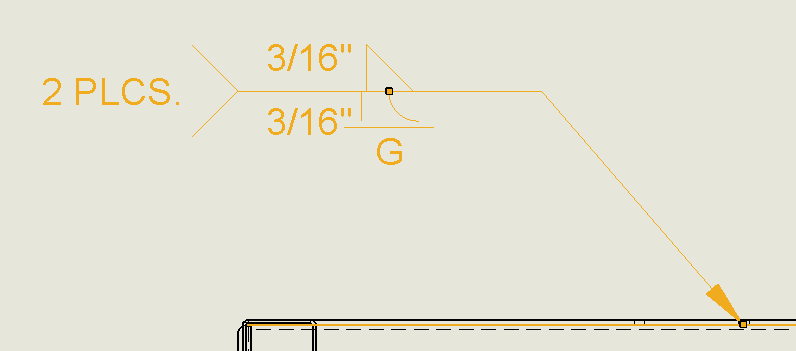