Algirdas13
Mechanical
- May 27, 2023
- 36
Hi everyone,
I'm planning to use fixed castor flanged wheels (1st picture bellow). The wheel itself has two bearings inside the wheel (2nd picture bellow). The rated load capacity for wheel is 3 tons. For example if I'm gonna load wheel with force that is not symmetrical in a view of wheel, does this mean that I cannot assume that wheel's capacity is 3 tons, but rather 1.5 tons (assuming that one bearing load capacity is 1.5 tons)? The load schemes are bellow.
I would be very grateful for any information.
I'm planning to use fixed castor flanged wheels (1st picture bellow). The wheel itself has two bearings inside the wheel (2nd picture bellow). The rated load capacity for wheel is 3 tons. For example if I'm gonna load wheel with force that is not symmetrical in a view of wheel, does this mean that I cannot assume that wheel's capacity is 3 tons, but rather 1.5 tons (assuming that one bearing load capacity is 1.5 tons)? The load schemes are bellow.
I would be very grateful for any information.
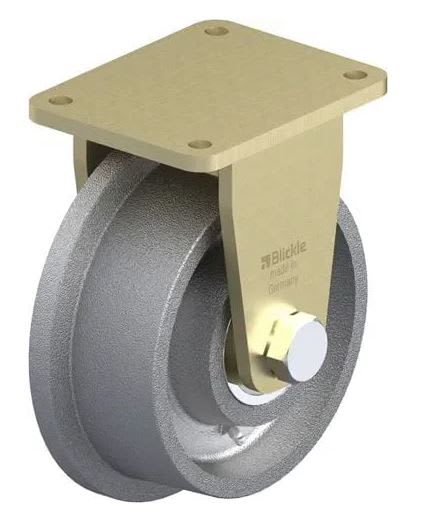
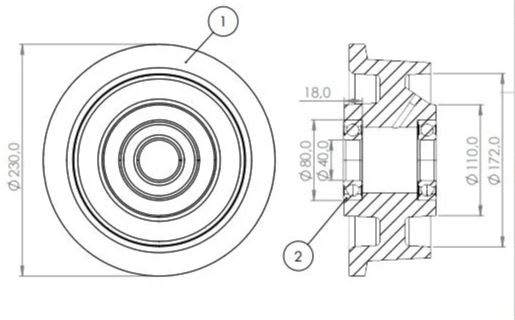
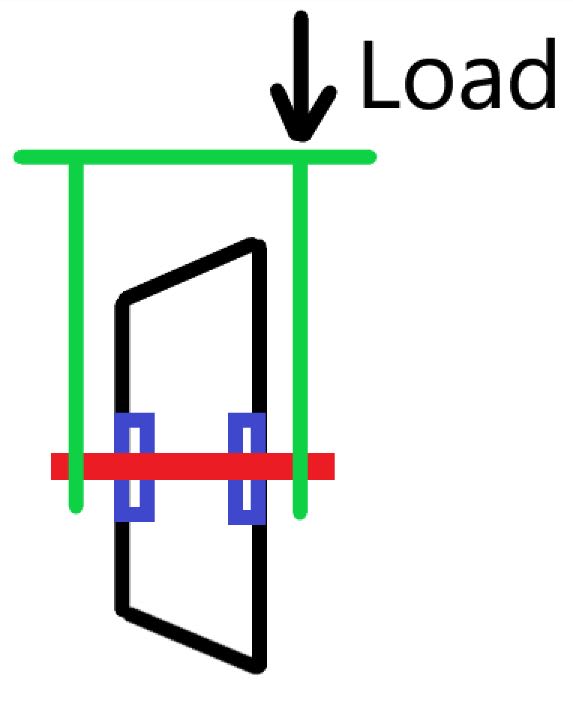