We build hundreds of 3" wide transfer belt assemblies every year. We have been building our own drive pulleys and lagging them with rough top belting but the whole pulley assembly has become quite expensive. I have been messing with a cast pulley with traction ribs cast in but by the time the foundry is done shot blasting the surfaces all sharp corners are rounded and the traction just isn't there. I need a quick and cheap way to add traction. The draft angle on the pulley face would make traditional lagging difficult. Is there a spray on grit (thermal spray) coating I could use? Urethane sleeve or band? It's 12" OD and I haven't fount a sleeve that large. All ideas are welcome.
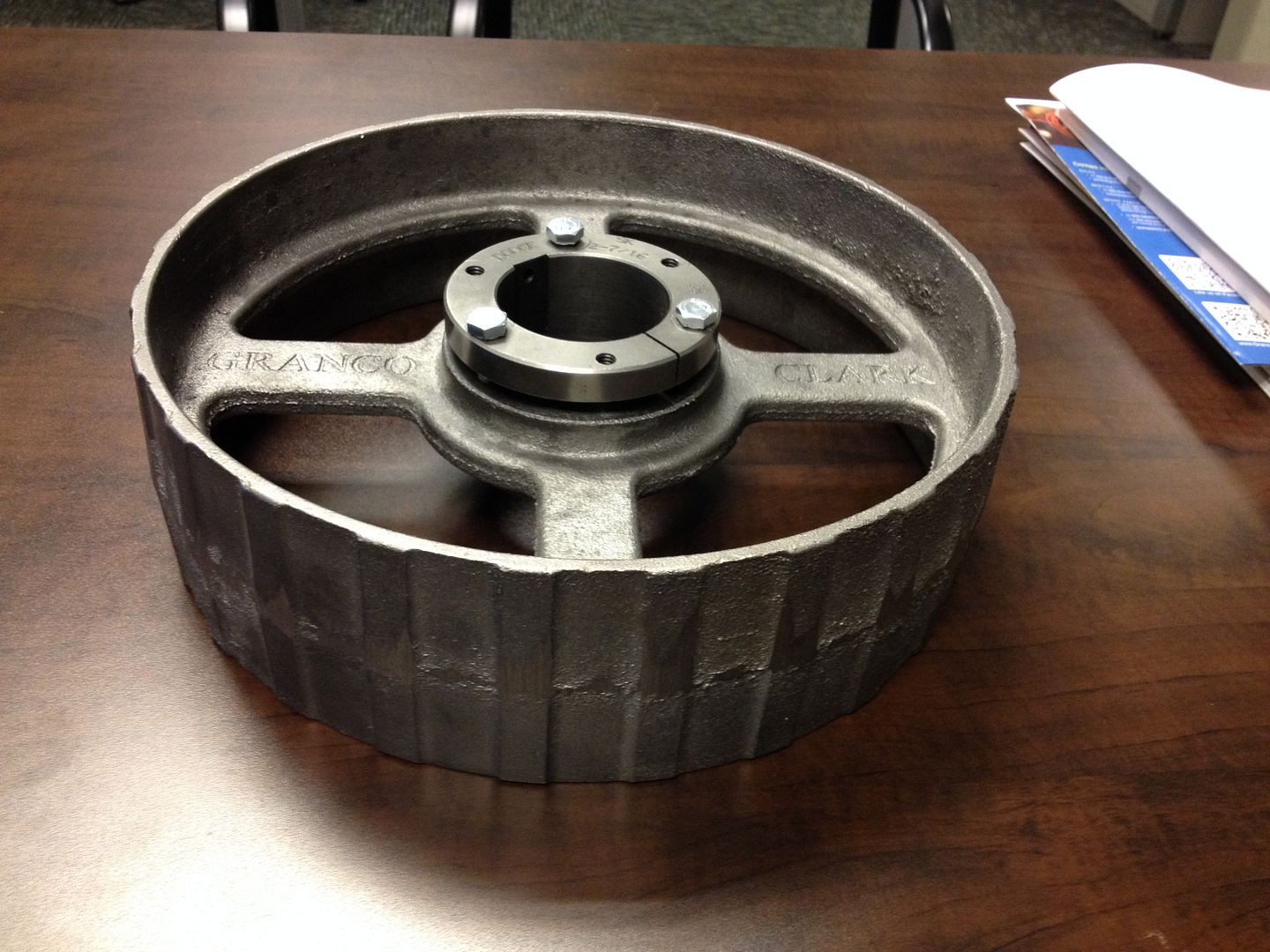