unclebensrice
Petroleum
Dear all,
how do you reconcile pic1 with pic2. Pic1 shows that at low flow (minimum flow) the DP across the control valve is high whereas in pic2 low flow is proportional to low DP across the control. can anyone please dispense my confusion over this ? thanks.
how do you reconcile pic1 with pic2. Pic1 shows that at low flow (minimum flow) the DP across the control valve is high whereas in pic2 low flow is proportional to low DP across the control. can anyone please dispense my confusion over this ? thanks.
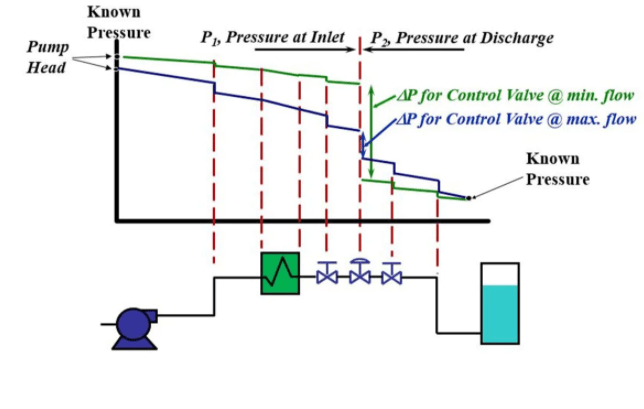
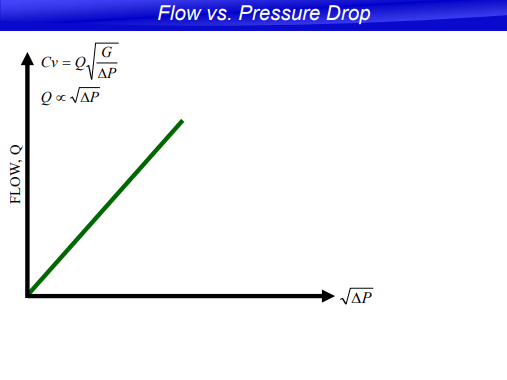