We just revamped two identical reciprocating compressors, from 3 stages high pressure to a low pressure sigle stage, in order meet the following:
Required Operating conditions:
Suction: 25-40 psig
Discharge: 120 psig
Flow (calculated with compressor brand software [CiP]): 2.4 (25 psig suction) - 4.0 MMSCFD (40 psig suction)
Two identical units were revamped, original frame CiP PHT-2 and CAT G3406TA were kept, replacing cylinders to go from 3 stg to a single stage unit, with two new 10" cylinders.
Current operating conditions:
Suction: 37 psig
Discharge: 100 psig
Flow measured with orifice plate and Nuflo Scanner 2000: 2.0 MMSCFD
With that suction pressure we should be getting at least 3.2 MMSCFD (volume pockets closed all the way, 1700 RPM. We are 1.2 MMSCFD short comparing the calculation from the software and the reality on site.
According to this conditions we should have a driver percent load of 66 %, therefore no engine overloading should be expected
Since the same thing is happening in both of the units we are considering the following:
1. Undersized scrubber. I made the calculations again and the scrubber is actually undersized, it is good for just about 3.0 MMSCFD @40 psig. However this should just affect the liquid separation efficiency, not the flow rate
2. Undersized piping: Cylinders flanges are 6", whereas suction piping is 4". This should just increase velocity and cause a dP from skid inlet to cylinder nozzle. This dP has been measured as 5 psig. We are still having enough pressure getting into the cylinders to get more flow, but still not meeting the flow.
3. Piping arrangement, as shown in the General Arrangement drawing below, the suction piping is not centered between the two cylinders, but just to one of them, however both cylinders have fixed capacity at certain pressure, so the flow should keep near to the same in both of them.
The performance run was reviewed by the compressor manufacturer, so the difference in flow rate has to be caused by something done during the revamp.
What is weird to me is that the suction pressure is not droping, meaning the cylinders are being filled, if they were not getting enough gas pressure this would drop until they are filled with the available source. We are having some compression valves high temperature, though.
What do you think the possible cause could be?
Performance run showing the expected flow rate:
I hope the information I provided is enough for you to analice and share your thoughts. Please let me know if I missed something else you need.
I appreciate your comments.
Required Operating conditions:
Suction: 25-40 psig
Discharge: 120 psig
Flow (calculated with compressor brand software [CiP]): 2.4 (25 psig suction) - 4.0 MMSCFD (40 psig suction)
Two identical units were revamped, original frame CiP PHT-2 and CAT G3406TA were kept, replacing cylinders to go from 3 stg to a single stage unit, with two new 10" cylinders.
Current operating conditions:
Suction: 37 psig
Discharge: 100 psig
Flow measured with orifice plate and Nuflo Scanner 2000: 2.0 MMSCFD
With that suction pressure we should be getting at least 3.2 MMSCFD (volume pockets closed all the way, 1700 RPM. We are 1.2 MMSCFD short comparing the calculation from the software and the reality on site.
According to this conditions we should have a driver percent load of 66 %, therefore no engine overloading should be expected
Since the same thing is happening in both of the units we are considering the following:
1. Undersized scrubber. I made the calculations again and the scrubber is actually undersized, it is good for just about 3.0 MMSCFD @40 psig. However this should just affect the liquid separation efficiency, not the flow rate
2. Undersized piping: Cylinders flanges are 6", whereas suction piping is 4". This should just increase velocity and cause a dP from skid inlet to cylinder nozzle. This dP has been measured as 5 psig. We are still having enough pressure getting into the cylinders to get more flow, but still not meeting the flow.
3. Piping arrangement, as shown in the General Arrangement drawing below, the suction piping is not centered between the two cylinders, but just to one of them, however both cylinders have fixed capacity at certain pressure, so the flow should keep near to the same in both of them.
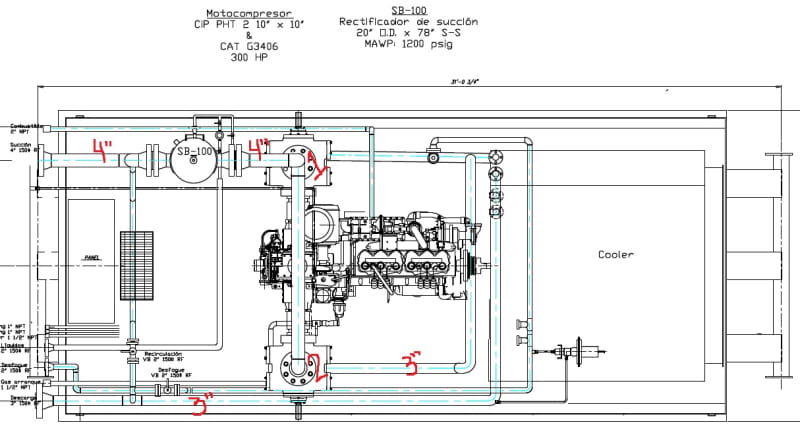
The performance run was reviewed by the compressor manufacturer, so the difference in flow rate has to be caused by something done during the revamp.
What is weird to me is that the suction pressure is not droping, meaning the cylinders are being filled, if they were not getting enough gas pressure this would drop until they are filled with the available source. We are having some compression valves high temperature, though.
What do you think the possible cause could be?
Performance run showing the expected flow rate:
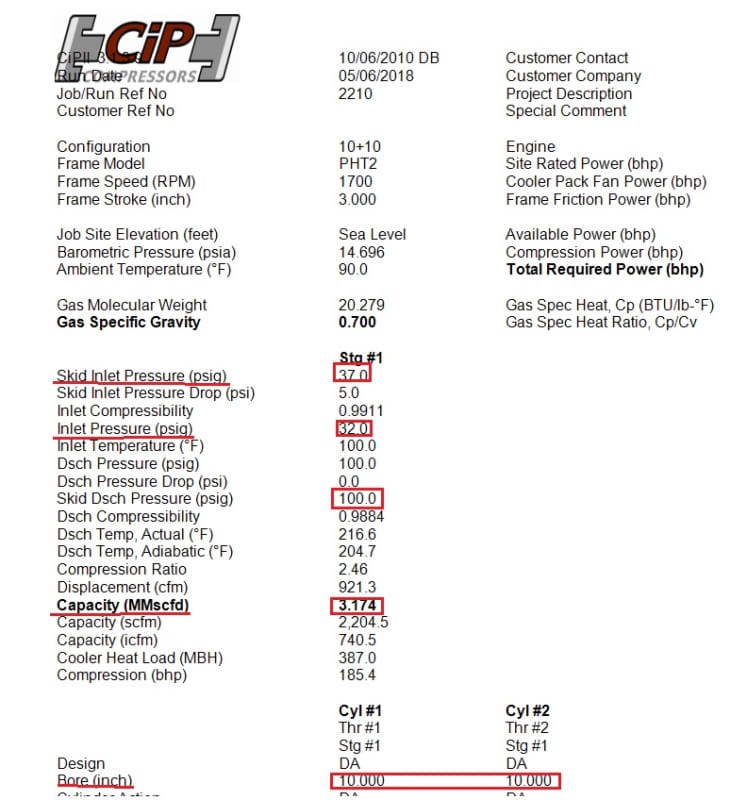
I hope the information I provided is enough for you to analice and share your thoughts. Please let me know if I missed something else you need.
I appreciate your comments.