Biltwell
Industrial
- Oct 18, 2023
- 31
Good day, I am new here and also not much a hydraulic expert but I have recently designed a valve body to be used on a horizontal band saw, This valve replaces a singular needle valve attached directly to the cylinder and now mounted about 36" from the cylinder. In the valve body is a needle cartridge valve with a toggle cartridge valve. The idea is to be able to adjust flow rate while also being able to lock the system completely. And it does work (sorta). When the valve is barely cracked open I seem to be having a flow issue. The fluid will flow for a couple of seconds then slow way down. And Ill have to keep opening the valve more and more until the flow rate is too high and that at that point it'll have consistent flow. I stuck to the same principles as the OEM valve and port sizes, IE 1/8 npt and 1/8 ID line. I've tried using 0w20 oil and that doesn't seem to increase flow rate at all. I could really use some advice/input on this one from someone with more experience than myself. Thank you!
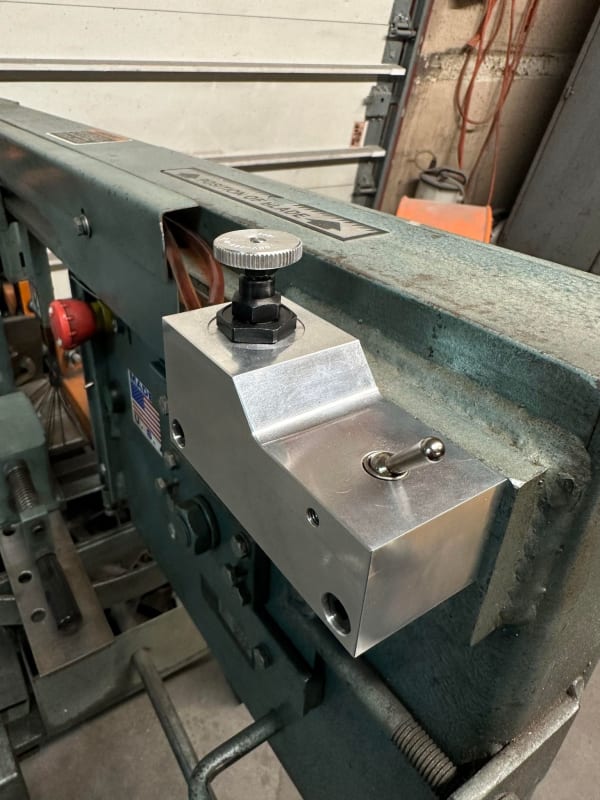
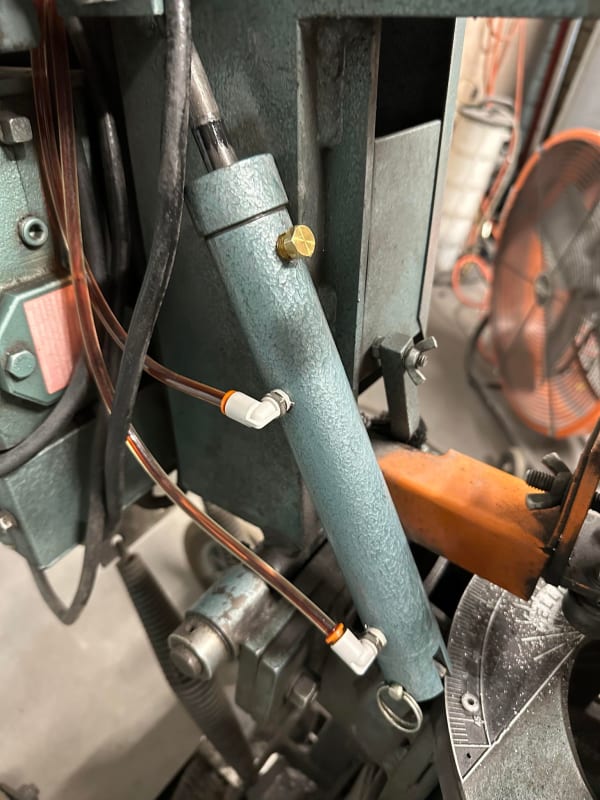