Rodger Furey
Mechanical
Question 1: Do I need a restriction in each branch of our plumbing?
According to a variety of sources, we should be limiting the velocity through our PVC pipes to 5 ft/sec.
5 ft/sec can be translated to GPM for each pipe size.
If I need to flow 3 GPM thru the branch to Tank A, I can pick a 1/2 IPS pipe and be below the 5 ft/sec … so far, so good.
The problem is the pressure drop from one end of the pipe to the other is usually much higher than needed, resulting in a much higher velocity than desired.
This has caused problems when we use some types of solenoid valves in each branch.
According to the Hazen-Williams equation, a 1/2 IPS pipe, 100 ft long will flow approx 5 GPM.
Handbook of PVC Pipe Design and Construction (uni-bell.org)
(I am also using the nomograph based on Hazen-Williams to check the calcs.)
Our branch pipes are much shorter … say, 10 ft long (equivalent length, factoring in fittings)
At 10 ft of length, Hazen-Williams returns a flow rate of almost 18 GPM, and a velocity of 26 ft/sec
In order to drop the velocity to 5 ft/sec, I only need approx 1 psi pressure drop.
It wouldn't be practical to reduce the pressure in the header to 1 psi.
Question 1.1: Therefore it seems like I should always be installing some sort of restriction in each branch to eat up 19 psi of pressure drop … a gate or needle valve?
Question 2: How do I achieve a 5 psi pressure drop across a solenoid valve?
I’m looking at this ASCO valve.
According to its data sheet, it needs a minimum of 5 psi operating pressure differential.
Well, if I install a 1/2 IPS valve (Cv 4.5) in my 1/2 IPS pipe, I would need to pass 10 GPM through that valve in order to achieve that pressure drop.
If I only pass 3 GPM (5 ft/sec), the pressure drop across the valve is only 0.4 psi.
Question 2.1: What am I doing wrong?
Thanks for any help!
According to a variety of sources, we should be limiting the velocity through our PVC pipes to 5 ft/sec.
5 ft/sec can be translated to GPM for each pipe size.

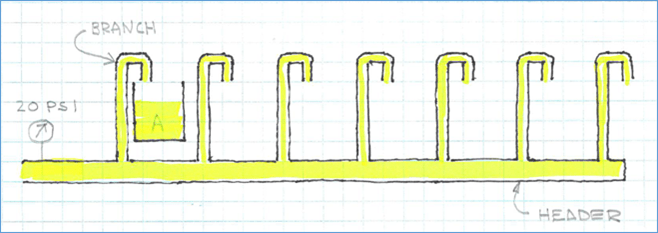
If I need to flow 3 GPM thru the branch to Tank A, I can pick a 1/2 IPS pipe and be below the 5 ft/sec … so far, so good.
The problem is the pressure drop from one end of the pipe to the other is usually much higher than needed, resulting in a much higher velocity than desired.
This has caused problems when we use some types of solenoid valves in each branch.

According to the Hazen-Williams equation, a 1/2 IPS pipe, 100 ft long will flow approx 5 GPM.
Handbook of PVC Pipe Design and Construction (uni-bell.org)
(I am also using the nomograph based on Hazen-Williams to check the calcs.)
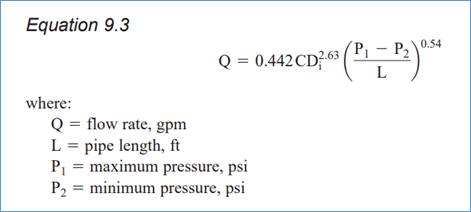
Our branch pipes are much shorter … say, 10 ft long (equivalent length, factoring in fittings)
At 10 ft of length, Hazen-Williams returns a flow rate of almost 18 GPM, and a velocity of 26 ft/sec
In order to drop the velocity to 5 ft/sec, I only need approx 1 psi pressure drop.
It wouldn't be practical to reduce the pressure in the header to 1 psi.
Question 1.1: Therefore it seems like I should always be installing some sort of restriction in each branch to eat up 19 psi of pressure drop … a gate or needle valve?
Question 2: How do I achieve a 5 psi pressure drop across a solenoid valve?
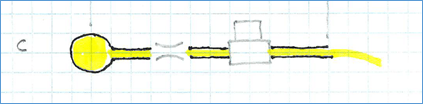
I’m looking at this ASCO valve.
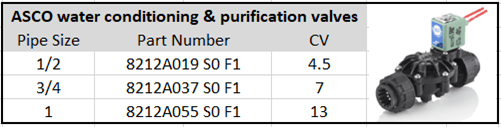
According to its data sheet, it needs a minimum of 5 psi operating pressure differential.
Well, if I install a 1/2 IPS valve (Cv 4.5) in my 1/2 IPS pipe, I would need to pass 10 GPM through that valve in order to achieve that pressure drop.
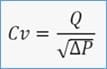
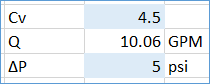
If I only pass 3 GPM (5 ft/sec), the pressure drop across the valve is only 0.4 psi.
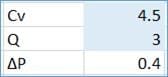
Question 2.1: What am I doing wrong?
Thanks for any help!