Sandychan
Structural
- Sep 25, 2015
- 22
Hello All,
I have a situation where I need to use an angle beam to support hollow core slabs. The angle beam will be welded to fixing plates that will be pre installed in a cast-in- place concrete wall. Each fixing plates have 4 bolts providing anchoring to the wall.
For the design, I have been suggested to consider 2 design stages, before and after concreat topping reaches its design strenght. The loads and design actions to the fixing plates of each stage are as followed:
Stage 1- Before the concrete topping reaches its design strenght
Only hollowed-core slab weight + concrete topping are concerned.
The vertical load in this stage will create shear and moment to the bolts of fixing plates.
Stage 2- After the concrete topping reaches its design strenght
Hollow core slab weight + concrete topping + super-imposed dead load + super-imposed live load are concerned.
The vertical load in this stage will create only shear to the bolts of fixing plates. This is because once the concrete in the gap between the angle beam and the hollow core slab ends reaches its design strength, the angle beam will not be able to tilt forward. As a result, it will not introduce tension to the fixing plate bolts.
Questions:
1. Do you agree that there will be on shear applying the bolts in Stage 2 because the concrete in the gap will prevent the angle beam to tilt forward?
2. I also need to consider robustness case where there will be a vertical load on the angle beam and tension the hook rebar. In case the concrete in the gap has reached the design strenght, then again it will be just shear from verical load applying to the bolts? In other words, the tension in the hook rebar will not do anything to the bolts?
Thank you so much in advance for your answers.
I have a situation where I need to use an angle beam to support hollow core slabs. The angle beam will be welded to fixing plates that will be pre installed in a cast-in- place concrete wall. Each fixing plates have 4 bolts providing anchoring to the wall.
For the design, I have been suggested to consider 2 design stages, before and after concreat topping reaches its design strenght. The loads and design actions to the fixing plates of each stage are as followed:
Stage 1- Before the concrete topping reaches its design strenght
Only hollowed-core slab weight + concrete topping are concerned.
The vertical load in this stage will create shear and moment to the bolts of fixing plates.
Stage 2- After the concrete topping reaches its design strenght
Hollow core slab weight + concrete topping + super-imposed dead load + super-imposed live load are concerned.
The vertical load in this stage will create only shear to the bolts of fixing plates. This is because once the concrete in the gap between the angle beam and the hollow core slab ends reaches its design strength, the angle beam will not be able to tilt forward. As a result, it will not introduce tension to the fixing plate bolts.
Questions:
1. Do you agree that there will be on shear applying the bolts in Stage 2 because the concrete in the gap will prevent the angle beam to tilt forward?
2. I also need to consider robustness case where there will be a vertical load on the angle beam and tension the hook rebar. In case the concrete in the gap has reached the design strenght, then again it will be just shear from verical load applying to the bolts? In other words, the tension in the hook rebar will not do anything to the bolts?
Thank you so much in advance for your answers.
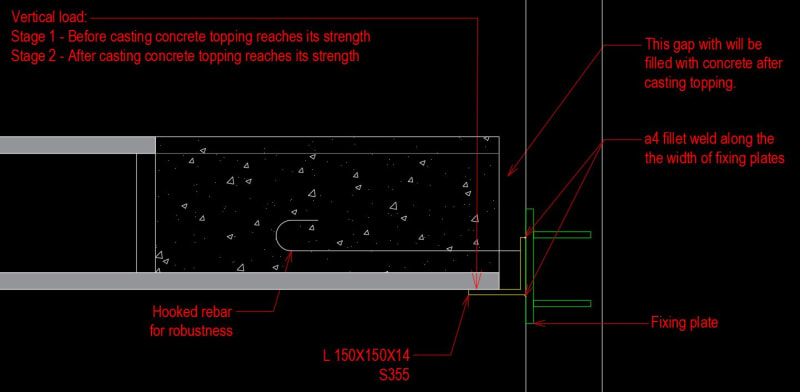