rmc2008
Structural
- Feb 10, 2020
- 2
I have two pumps that each weighs 6850 kgs (15100 lbs) and runs at 3600 RPM. Owing to certain restrictions the foundation on which my pump sits is only 650 mm thick (13.3m x 9.35m) with the two pumps centered on a 7.7m x 6.5m x 150mm thk pedestal. This big pile cap 13.3 x 9.35 is supported on 21 nos -500 dia concrete piles 10 m long embedment.The weight of foundation is approximately 15 times weight of pumps together. Dynamic analysis of the foundation was performed using DYNA. In the machine performance curve for a node at the motor location the resonance frequency was found to occur at 100% normal operating speed. See red curve in attachment. Since the foundation is so much heavier than the pumps should I be concerned about this?
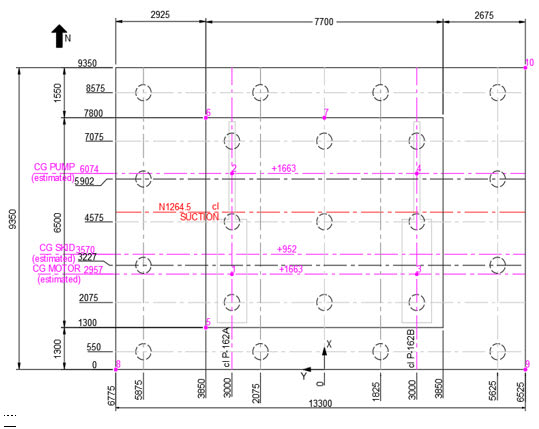