Hi guys & girls,
I'm trying to enter the world of fracture mechanics of pressure vessels using FEAs. The first challenge I've encountered now is how to include residual stresses at weld beads?
An example of what a residual stress may look like (from API 579, Annex 9D):
I've also attached a simple ANSYS file with a shell and simple elliptical crack.
So, how does one go about applying residual stresses in a finite element model before doing a crack analysis? Is it possible to insert the residual stresses as an initial condition? To start of simple, I'd like to first have a uniform tensile stress of 10 MPa in the vertical and circumferential direction at t0 (before fracture mechanics assessment).
Julian
I'm trying to enter the world of fracture mechanics of pressure vessels using FEAs. The first challenge I've encountered now is how to include residual stresses at weld beads?
An example of what a residual stress may look like (from API 579, Annex 9D):
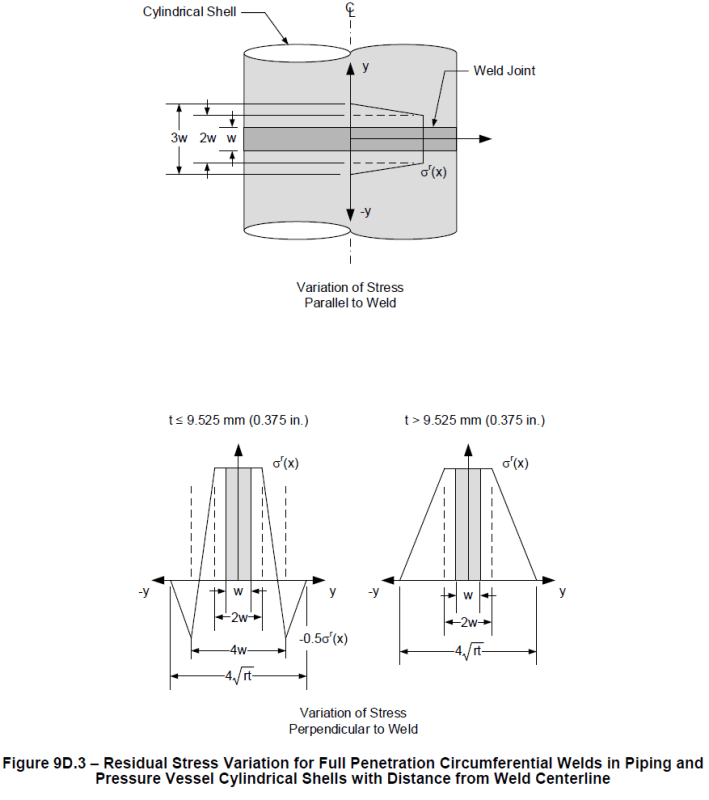
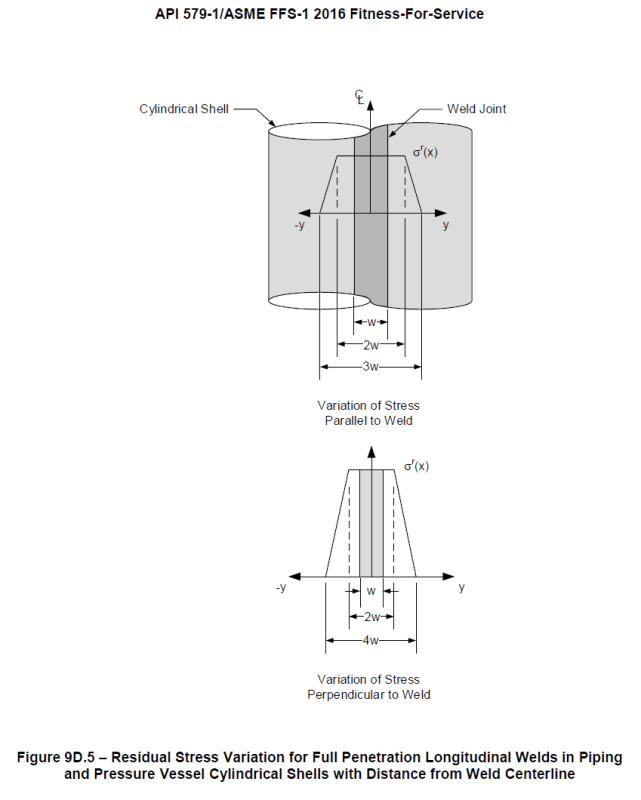
I've also attached a simple ANSYS file with a shell and simple elliptical crack.
So, how does one go about applying residual stresses in a finite element model before doing a crack analysis? Is it possible to insert the residual stresses as an initial condition? To start of simple, I'd like to first have a uniform tensile stress of 10 MPa in the vertical and circumferential direction at t0 (before fracture mechanics assessment).
Julian