rollingcloud
Aerospace
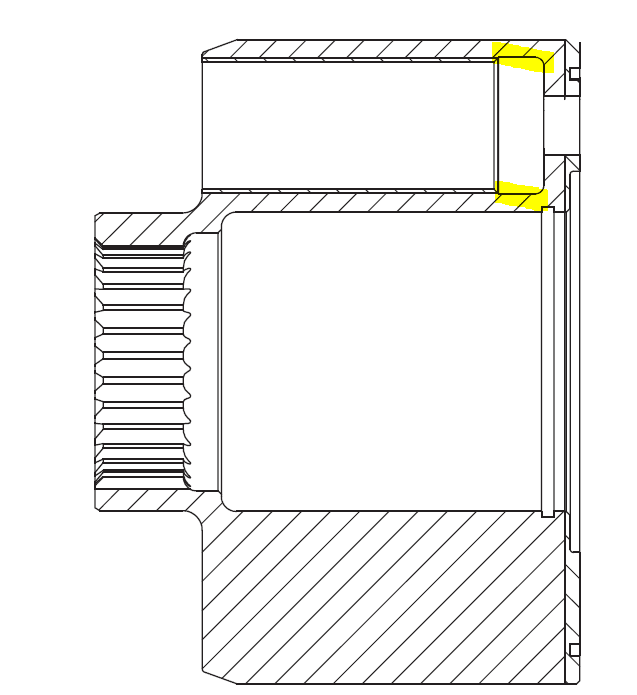
Is this for thermal expansion of the fluid? The piston has a constant size, so when it reaches the bottom, there would be a tiny gap around the end of the piston. Below is an Axial Piston Pump that also has an expansion in the displacement chamber, but it's located in the middle of the chamber. not sure if they share a similar function.
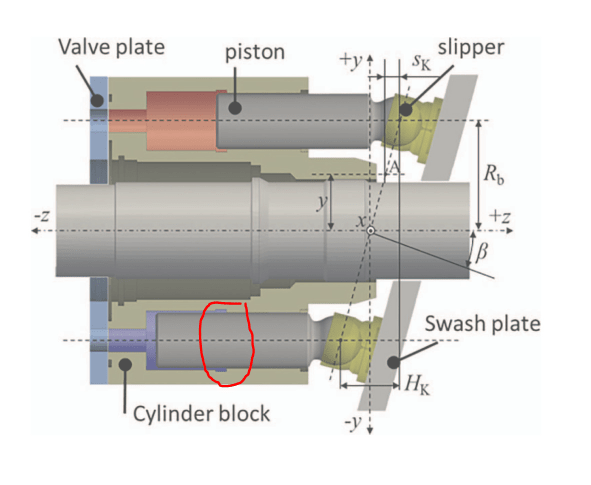