Kall545
Agricultural
- Oct 12, 2016
- 28
Gap or no gap on sheet metal bends ?
Is it ok to make bends without gaps like in photo or is it wrong ?
Is it ok to make bends without gaps like in photo or is it wrong ?
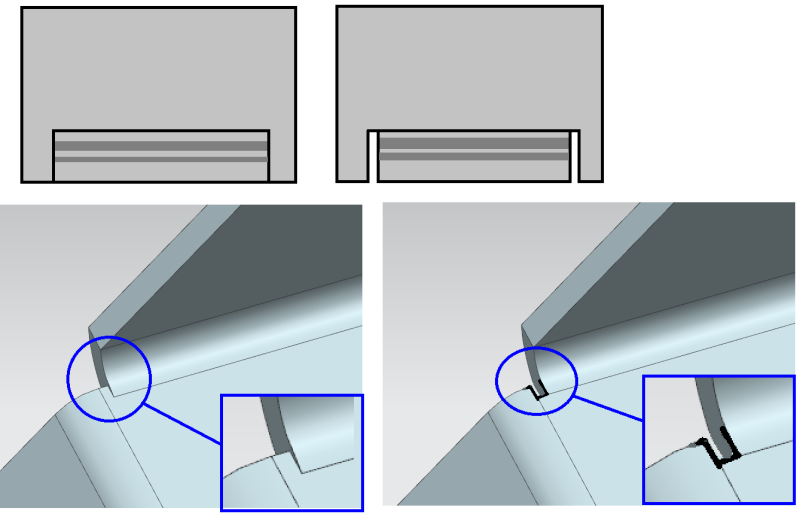
Follow along with the video below to see how to install our site as a web app on your home screen.
Note: This feature may not be available in some browsers.