Hello everyone I have a question about the design forces used for gas pipes supports.
The pipes undergo equal tensile forces Which they cancel out at the support F and -F. However, these forces get transmitted to the support, even when they also cancel out, the support sees the stresses. Is it better to design for the force F as it didn’t cancel out. Or what design procedure would you use?
Thank you!
Thank you.
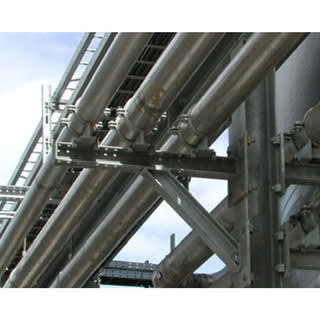
The pipes undergo equal tensile forces Which they cancel out at the support F and -F. However, these forces get transmitted to the support, even when they also cancel out, the support sees the stresses. Is it better to design for the force F as it didn’t cancel out. Or what design procedure would you use?
Thank you!
Thank you.