leon_har_dt
Mechanical
- Nov 3, 2022
- 27
Hi!, i'm a new member.
First, i want to make a recognition and gratitude to this forum and the people who participate in. I always can find some guide to solve my problems and that it's thanks to the community.
I'm facing a problem wich I could not found a guide by searching it here (beside that english it's not my first language i did my best effort)
In my first year of engineer(mechanical) i had to design two heat exchangers who work with water(shell) and oil(tubes)(water heats the oil).
The design temperature and pressure it's 266F(130C) and 145psi(10bar)(for both circuits). I selected a PFTE gasket chesterton ecs-b e=1/16" for a B16.5 Slip on flange SA182 F304L.(the tubesheet was made of a blind flange, same characteristics). The HX was tested in the shop at 13bar(188psi) and didn't present leak
The problem begins when the customer was running their test and one of the HX leaked in the flange joint, we change the gasket days latter. The other one didn't present any leak and was use in the plant operation. Then the second one present leak, and analyzing the gasket(picture down below) it fail in a very similar way than the other
The customer said that the circuit consist of a recirculation circuit 1 bar pressure, and an impulsive circuit 7bar pressure (maintaining some vessel level of fluid)
Here you can see the deformation of the gasket when the second HX leaked days latter when then plant return to operation(this gasket was not the one who was replace). Red lines pictures the original form of the gasket.
After writing the context. ¿Could this effect be caused by water hammer or surge when the system change from 1bar to 7 bar or vice versa?
or ¿could be when the plant return the operation and the sudden change in pressure deform the gasket?
What else could be the reason?
I'm analyzing the change of gasket material and even the type of gasket being compatible with oil and B16.5
I would be grateful if you could expand my mind in this problem
L.
First, i want to make a recognition and gratitude to this forum and the people who participate in. I always can find some guide to solve my problems and that it's thanks to the community.
I'm facing a problem wich I could not found a guide by searching it here (beside that english it's not my first language i did my best effort)
In my first year of engineer(mechanical) i had to design two heat exchangers who work with water(shell) and oil(tubes)(water heats the oil).
The design temperature and pressure it's 266F(130C) and 145psi(10bar)(for both circuits). I selected a PFTE gasket chesterton ecs-b e=1/16" for a B16.5 Slip on flange SA182 F304L.(the tubesheet was made of a blind flange, same characteristics). The HX was tested in the shop at 13bar(188psi) and didn't present leak
The problem begins when the customer was running their test and one of the HX leaked in the flange joint, we change the gasket days latter. The other one didn't present any leak and was use in the plant operation. Then the second one present leak, and analyzing the gasket(picture down below) it fail in a very similar way than the other
The customer said that the circuit consist of a recirculation circuit 1 bar pressure, and an impulsive circuit 7bar pressure (maintaining some vessel level of fluid)
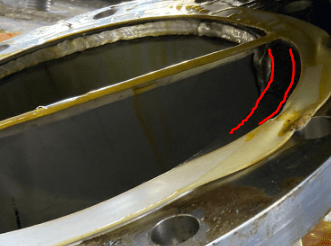
Here you can see the deformation of the gasket when the second HX leaked days latter when then plant return to operation(this gasket was not the one who was replace). Red lines pictures the original form of the gasket.
After writing the context. ¿Could this effect be caused by water hammer or surge when the system change from 1bar to 7 bar or vice versa?
or ¿could be when the plant return the operation and the sudden change in pressure deform the gasket?
What else could be the reason?
I'm analyzing the change of gasket material and even the type of gasket being compatible with oil and B16.5
I would be grateful if you could expand my mind in this problem
L.