Hi all,
My coworkers and I can not agree on the proper GD&T for this situation:
We have a shaft, with an offset blind hole in it. There are 2 threaded holes which run perpendicular to the hole. I need the GD&T to indicate that the set screw holes need to go through the thickest section of the part, otherwise the screws used here will fail in various ways.
Due to the constraints of the design, we cannot change the thread pitch of the screw holes.
This is what I have proposed, but I also feel at the same time that it's overkill. I'm also unsure if my perpendicularity callout on the threaded holes makes sense, since it references a derived median line datum, and a feature of size datum that is parallel to first.
And one colleague takes issue with the datum scheme, saying that the shaft should be the primary or secondary datum.
I'm curious to hear what solutions come to mind.
My coworkers and I can not agree on the proper GD&T for this situation:
We have a shaft, with an offset blind hole in it. There are 2 threaded holes which run perpendicular to the hole. I need the GD&T to indicate that the set screw holes need to go through the thickest section of the part, otherwise the screws used here will fail in various ways.
Due to the constraints of the design, we cannot change the thread pitch of the screw holes.
This is what I have proposed, but I also feel at the same time that it's overkill. I'm also unsure if my perpendicularity callout on the threaded holes makes sense, since it references a derived median line datum, and a feature of size datum that is parallel to first.
And one colleague takes issue with the datum scheme, saying that the shaft should be the primary or secondary datum.
I'm curious to hear what solutions come to mind.
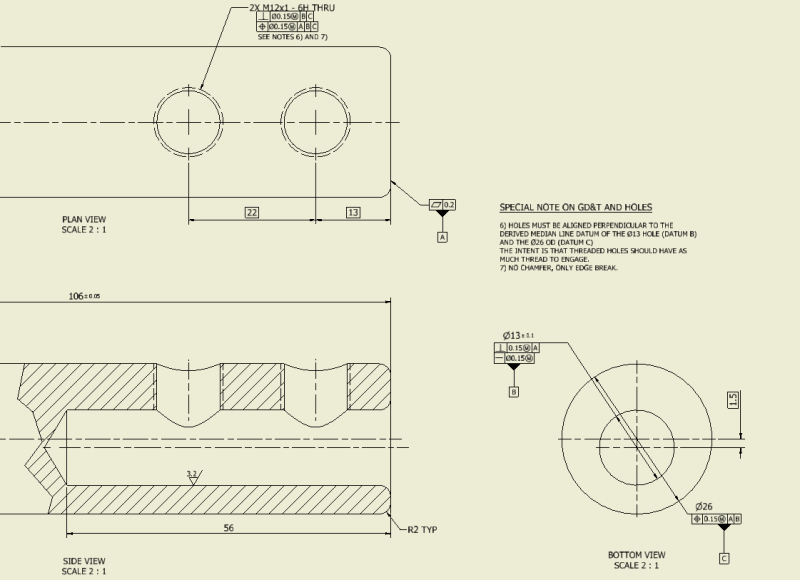