aammons2
Mechanical
- Dec 5, 2022
- 2
Hello,
I was hoping to get some guidance with GD&T as this is my first crack at it out of school. This is a gage that will have a precision ground pin coming in from the top to check for a hole location in a cylindrical part w.r.t a dimple on the bottom side of that part. Hole and dimple are in line with one another. Have I called these out properly? Both the top hole in the gage w.r.t datums A, B, C and the hole in the bottom of the gage that I want to be concentric with the top hole.
Thank You
I was hoping to get some guidance with GD&T as this is my first crack at it out of school. This is a gage that will have a precision ground pin coming in from the top to check for a hole location in a cylindrical part w.r.t a dimple on the bottom side of that part. Hole and dimple are in line with one another. Have I called these out properly? Both the top hole in the gage w.r.t datums A, B, C and the hole in the bottom of the gage that I want to be concentric with the top hole.
Thank You
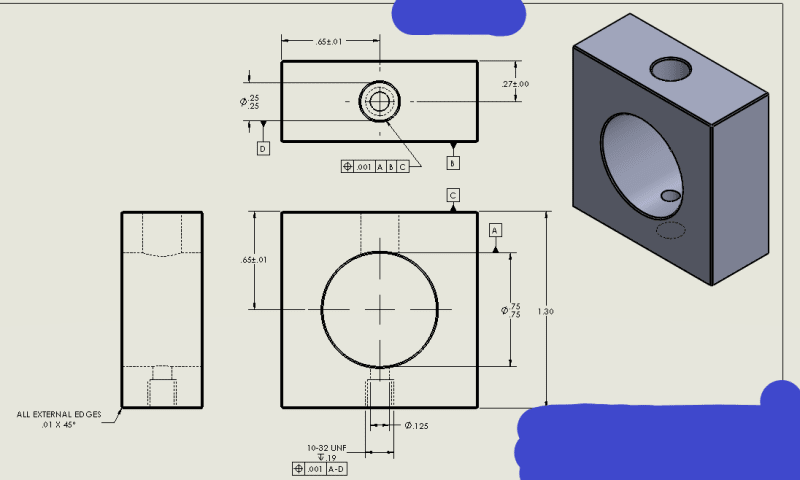