Qcprick63
Industrial
- Mar 7, 2023
- 34
Not a fan of this type of callout.
I ran a circle at the far edges of both bores then recalled into a 3d line . Put a few more circles on both diameters and asked for runout back to the 3D line. I guess I report the highest runout value? Is that correct or is there a better way??
I ran a circle at the far edges of both bores then recalled into a 3d line . Put a few more circles on both diameters and asked for runout back to the 3D line. I guess I report the highest runout value? Is that correct or is there a better way??
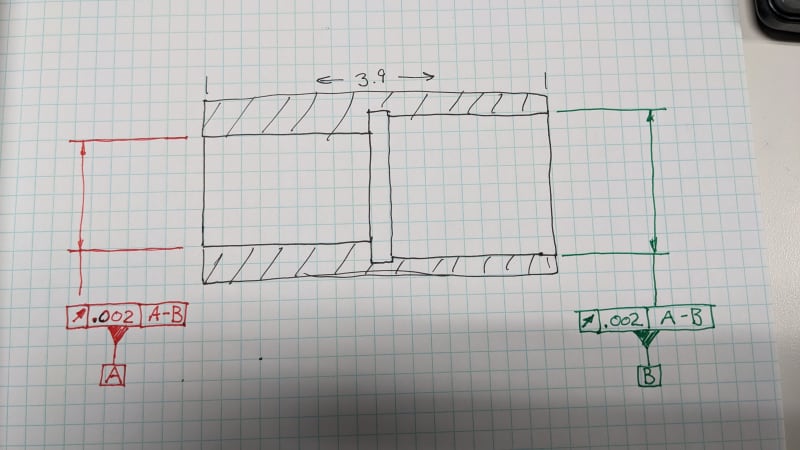