Hello all, I'm hoping you can help me determine a reasonable strategy to control the amount of allowable twist in a rectangular prismatic shape?
If you look at the following picture, I sometimes deal with the types of parts that can have twist induced by various means of manufacturing. This is the type of twist that can be recognized by putting the part on a granite slab, and noticing one corner of the part will rise up from the slab when it's opposite diagonal corner is pushed down to contact the slab. In fact, it's quite practical for us to measure this twist by inserting feeler gauges into the gap between the slab and the rising corner. So we have a reasonable way to check and measure this condition, I'm just looking for advice on datum placement and feature control designation. Perhaps parallelism?
If you look at the following picture, I sometimes deal with the types of parts that can have twist induced by various means of manufacturing. This is the type of twist that can be recognized by putting the part on a granite slab, and noticing one corner of the part will rise up from the slab when it's opposite diagonal corner is pushed down to contact the slab. In fact, it's quite practical for us to measure this twist by inserting feeler gauges into the gap between the slab and the rising corner. So we have a reasonable way to check and measure this condition, I'm just looking for advice on datum placement and feature control designation. Perhaps parallelism?
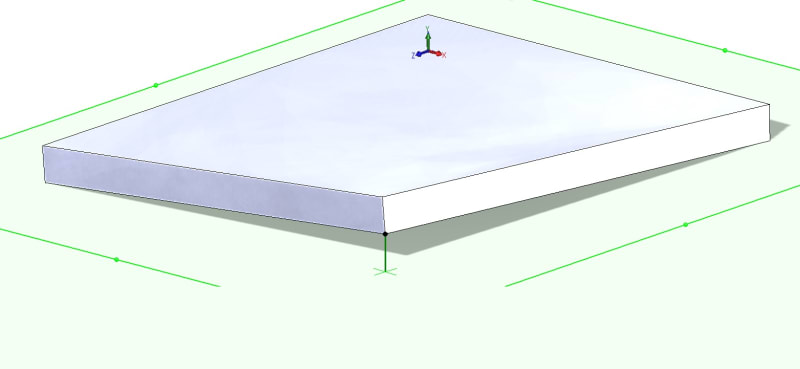