Hi all , i have a problem where my structure is a combination of glass material and aluminium. The glass is glued to the aluminum frame, also fastened to the frame . so basically the glass is fastened and glued to the aluminum frame.i am trying to simulate this on FEMAP. But when i run a glue contact the fasteners(CBUSH) will never see loads because the primary load path is always the glue connection.
1)can someone suggest me ideas on how i can post process the glue connection?
2)what loads can be used on femap to estimate the glue failure? .
3) in my case where glue and fasteners are working together, how to model to accurately estimate fastener loads ?
1)can someone suggest me ideas on how i can post process the glue connection?
2)what loads can be used on femap to estimate the glue failure? .
3) in my case where glue and fasteners are working together, how to model to accurately estimate fastener loads ?
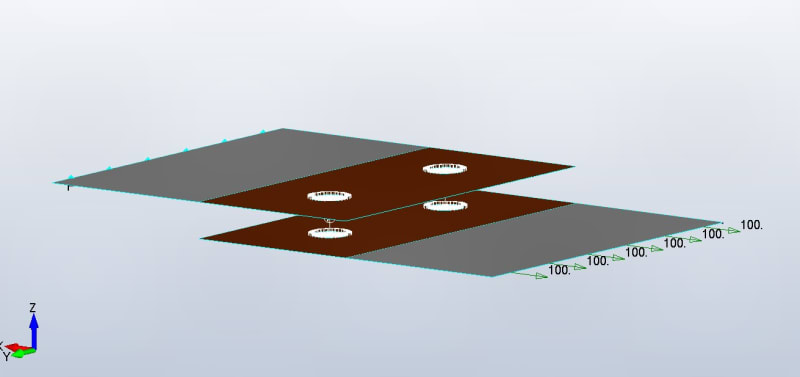