Bhotar3
Civil/Environmental
- May 6, 2013
- 62
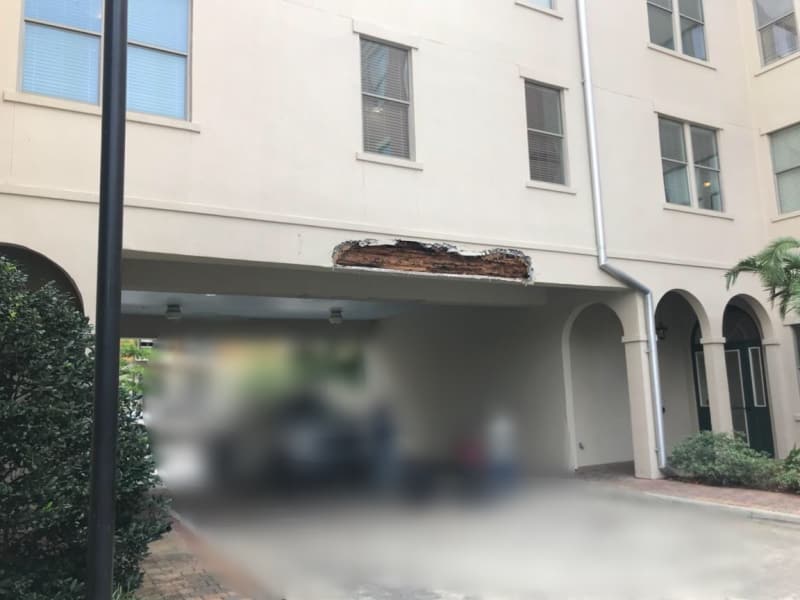
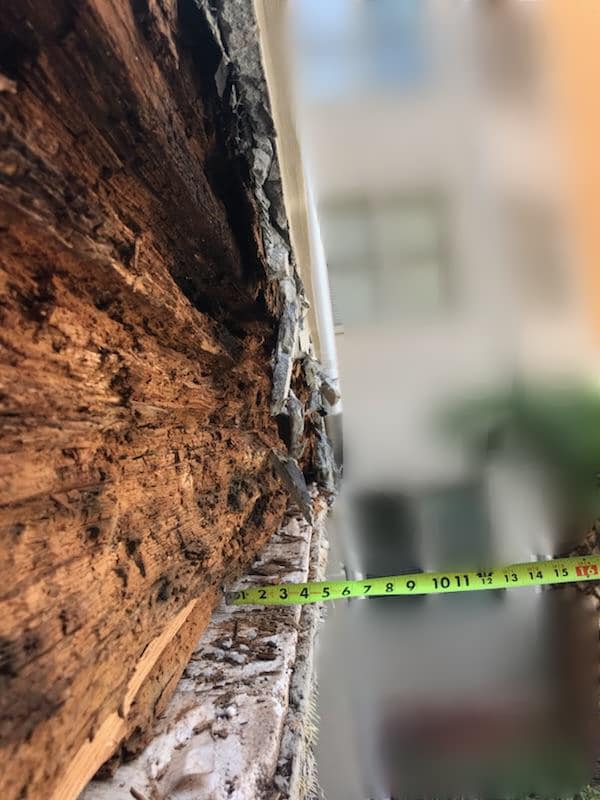
I’ve been tasked to Analyze and give a Engineering Judgement on a damaged glulam beam for an apartment complex. I wanted to get a feel for potential solutions from the board here, as I don’t have a ton of experience dealing with Timber design.
A truck didn’t clear the bottom of the beam, and At first glimpse, there is pretty significant damage to the structure. It looks like it gouged out a pretty decent chuck of the member. Also, it looks like there has been some significant moisture damage now that the beam is exposed.
Are there any potential retrofit ideas here? Could they potentially bolt metal plates on both sides of the affected portion? I would assume you can not cut out and splice in a new beam just at the damaged location (or maybe you can and just need to design significant splice connections).
Or is a complete replace in kind the only realistic option? It would require substantial bracing, as this complex is 3 stories.