EngDM
Structural
- Aug 10, 2021
- 682
I see guardrail connections with 2 bolts/fasteners quite frequently, but I'm not sure exactly how to analyze these. I've tried putting it into Simpson's anchor designer but it can't find equilibrium. I'm sure these connections are okay since they are used often.
Where does the moment go when anchors are in a line? There is no T/C moment arm between the two.
Profis seems to be able to model this and determine loads, however it still appears to fail since the compressive strength in the concrete under the compressive zone is exceeded. So how do these two bolt concrete connections ever work, since there is no way 55MPa concrete is specified for this.
I checked in DG1 but couldn't find anything with 2 anchors in a line perpendicular to the moment direction.
Where does the moment go when anchors are in a line? There is no T/C moment arm between the two.
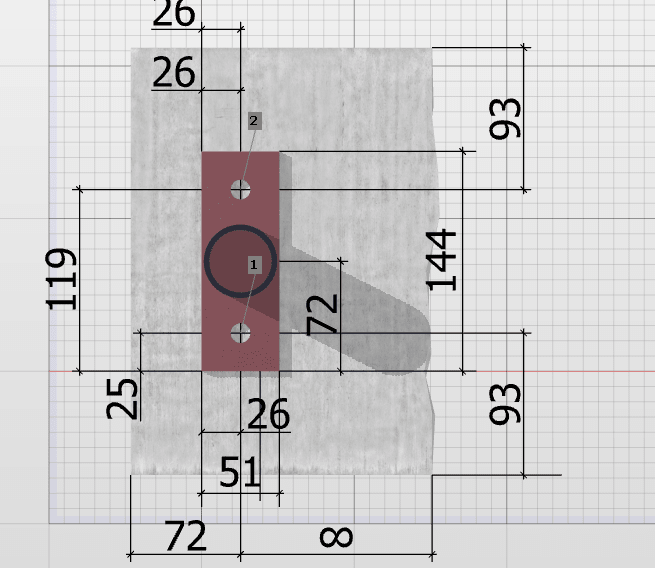
Profis seems to be able to model this and determine loads, however it still appears to fail since the compressive strength in the concrete under the compressive zone is exceeded. So how do these two bolt concrete connections ever work, since there is no way 55MPa concrete is specified for this.
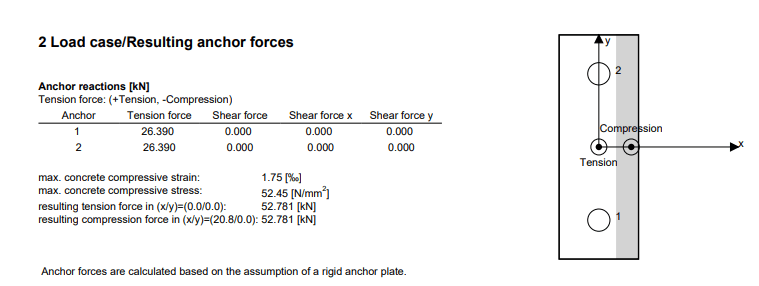
I checked in DG1 but couldn't find anything with 2 anchors in a line perpendicular to the moment direction.