Hi,
I have a situation where in order to take out the lateral thrust onto the S.O.G and not design huge footings for that moment (Horiz. Load* Height from top of footing to U/S of base plate), attached the snip below for reference...... If I place my hair pins at the bottom of my col. and connect the column to S.O.G, can I not worry about the Lateral thrust?, its a PEB portal frame. Thank you! for responses
I have a situation where in order to take out the lateral thrust onto the S.O.G and not design huge footings for that moment (Horiz. Load* Height from top of footing to U/S of base plate), attached the snip below for reference...... If I place my hair pins at the bottom of my col. and connect the column to S.O.G, can I not worry about the Lateral thrust?, its a PEB portal frame. Thank you! for responses
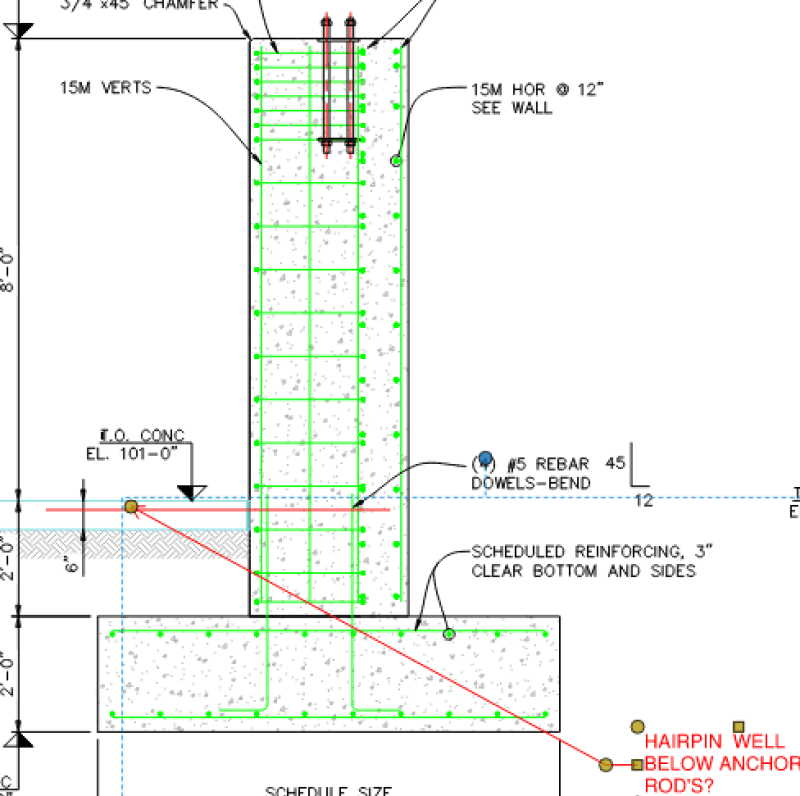