Hi,
I'm looking at a handrail stanchion type baseplate (where the two anchor bolts are perpendicular to the bending moment).
I'm used to designing moment connections by resolving the bending moment into a tension and compression force and then using this tension force to calculate the size of the base plate to resist bending. In this case, however, there is only one row of bolts in the direction of the bending moment.
I've assumed that the plate will resist the full bending moment in this case. Can someone please verify what I have done:
M* = V x e = 3.2kN x 0.4m = 1.28kNm
Assume base plate (220mm x 100mm x 10THK) is resisting this bending moment:
ϕM = 0.9 x fy x Z = 0.9 x 250 x bd²/4 = 0.9 x 250 x (220 x 10²/4) = 1.24kNm < M*
Is my method conservative? Is there any other way to calculate the plate bending capacity for this scenario?
Thanks!
I'm looking at a handrail stanchion type baseplate (where the two anchor bolts are perpendicular to the bending moment).
I'm used to designing moment connections by resolving the bending moment into a tension and compression force and then using this tension force to calculate the size of the base plate to resist bending. In this case, however, there is only one row of bolts in the direction of the bending moment.
I've assumed that the plate will resist the full bending moment in this case. Can someone please verify what I have done:
M* = V x e = 3.2kN x 0.4m = 1.28kNm
Assume base plate (220mm x 100mm x 10THK) is resisting this bending moment:
ϕM = 0.9 x fy x Z = 0.9 x 250 x bd²/4 = 0.9 x 250 x (220 x 10²/4) = 1.24kNm < M*
Is my method conservative? Is there any other way to calculate the plate bending capacity for this scenario?
Thanks!
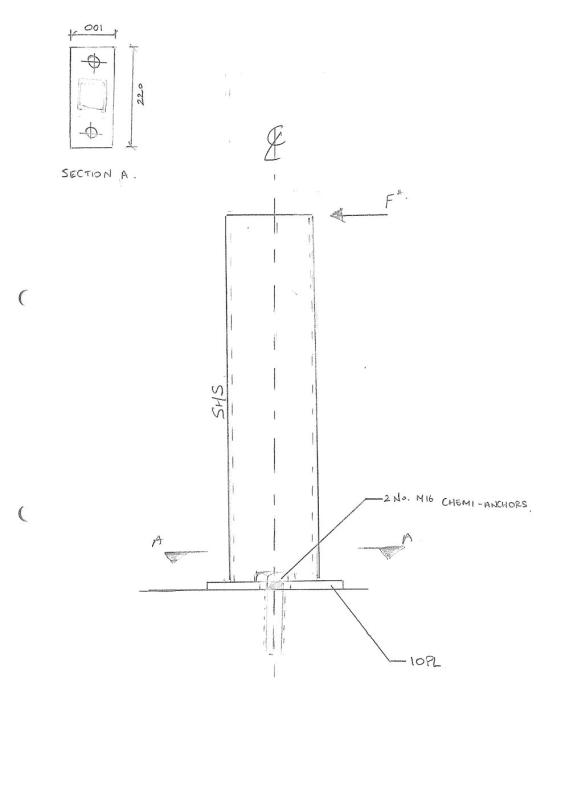