JackRu
Electrical
- Sep 22, 2020
- 8
Hi all,
So I am trying to replicate a tool known as an increment borer. It is a hollow shaft with hollow cutting threads on one end meant to screw into live wood and extract a 16"-long core sample. I have been told by their engineers that the borer is made out of Uddeholm Rigor (XW-10) steel, also known as A2 tool steel and is hardened to 48 HRC. The best steel I can find in the dimensions of the shaft (0.375" OD by 0.259" ID) is 4130. Unfortunately I do not have access to a gun drill able to drill out solid steel rod to such lengths, so I am limited to 4130 at the moment. I created a table below with my torque and angular deflection calculations based on different steels in various conditions:
It appears that quenching 4130 at 1575°F and tempering it at 400°F would achieve similar yield and ultimate torque values to the actual material used, AISI A2. The manufactures of the increment borer claim that their tool can withstand up to 90 ft-lbs of torque (field tested). My only concern is that 4130 would become too brittle at such a low tempering temperature (near its maximum hardness) and thus will not have enough tensile toughness to withstand such a high torque given the angular deflection. Any thoughts on this? I also know that for 4130 tempered at 400°F, the elongation in 2" is ~15%, its reduction in area is ~42%, and its Izod impact is ~31 ft-lb/in.
Is there a reasonable way to calculate its maximum permissible angular deflection based on the applied torque and toughness of 4130 after heat treating at these temperatures?
Thanks,
Jack
So I am trying to replicate a tool known as an increment borer. It is a hollow shaft with hollow cutting threads on one end meant to screw into live wood and extract a 16"-long core sample. I have been told by their engineers that the borer is made out of Uddeholm Rigor (XW-10) steel, also known as A2 tool steel and is hardened to 48 HRC. The best steel I can find in the dimensions of the shaft (0.375" OD by 0.259" ID) is 4130. Unfortunately I do not have access to a gun drill able to drill out solid steel rod to such lengths, so I am limited to 4130 at the moment. I created a table below with my torque and angular deflection calculations based on different steels in various conditions:
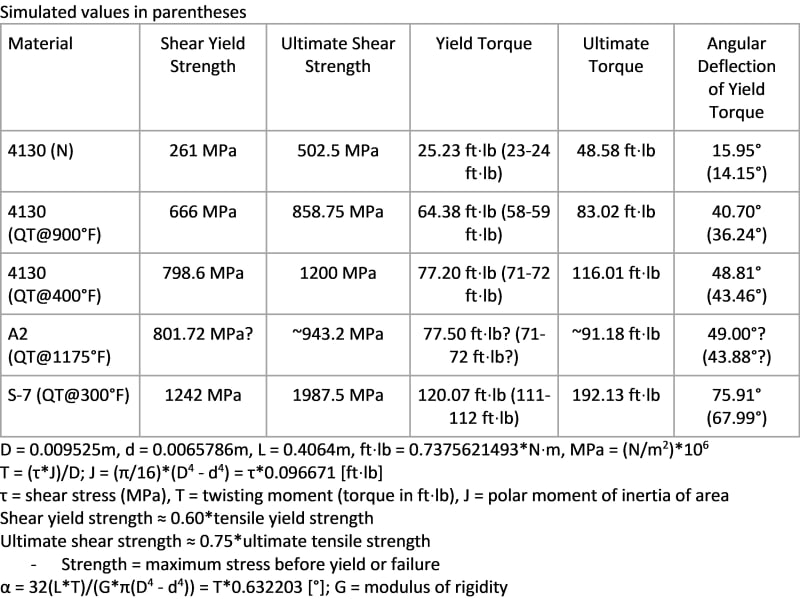
It appears that quenching 4130 at 1575°F and tempering it at 400°F would achieve similar yield and ultimate torque values to the actual material used, AISI A2. The manufactures of the increment borer claim that their tool can withstand up to 90 ft-lbs of torque (field tested). My only concern is that 4130 would become too brittle at such a low tempering temperature (near its maximum hardness) and thus will not have enough tensile toughness to withstand such a high torque given the angular deflection. Any thoughts on this? I also know that for 4130 tempered at 400°F, the elongation in 2" is ~15%, its reduction in area is ~42%, and its Izod impact is ~31 ft-lb/in.
Is there a reasonable way to calculate its maximum permissible angular deflection based on the applied torque and toughness of 4130 after heat treating at these temperatures?
Thanks,
Jack