Anthony_J
Mechanical
- Aug 28, 2024
- 9
Hello all,
I have a unique situation where I work at a plant that is equipped with air handling units that are so strong that it makes egress from some doors up to 100 lbs to open. Long story short, I've been tasked with providing assistance to drop this force down to NFPA-101 requirements of 30 lbs force to open it.
The device below is similar to what I'm looking at doing. You pull on the handle and it reacts with the wedge on the door frame, popping the door free. I preferable would like to start with a purchase item that I could modify but I can find nothing like this. Has anyone had to develop an item like this before?
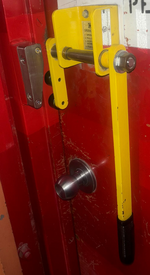
~Anthony
I have a unique situation where I work at a plant that is equipped with air handling units that are so strong that it makes egress from some doors up to 100 lbs to open. Long story short, I've been tasked with providing assistance to drop this force down to NFPA-101 requirements of 30 lbs force to open it.
The device below is similar to what I'm looking at doing. You pull on the handle and it reacts with the wedge on the door frame, popping the door free. I preferable would like to start with a purchase item that I could modify but I can find nothing like this. Has anyone had to develop an item like this before?
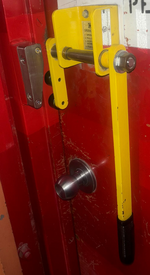
~Anthony