Sajjad2164
Mechanical
- Dec 22, 2015
- 55
Hello friends, I have reached an arrangement consisting of two furnaces and thirteen return fire tubes. The general duty of the heater is 10 MW. The heater follows a natural draft circulation. I want to put four burners into each furnace to gain the task. Is it possible?
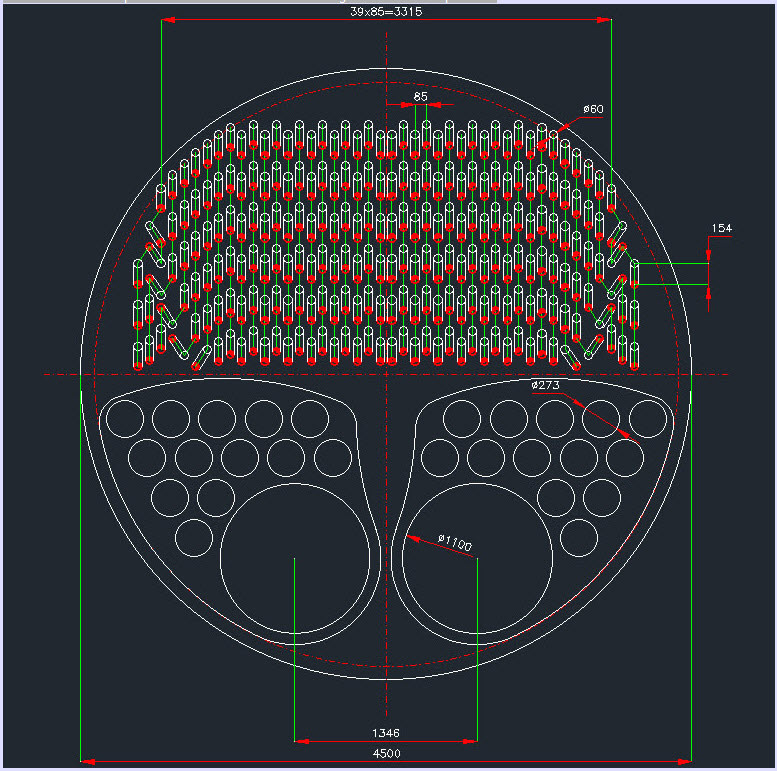